Water intrusion around windows is a common issue that can lead to serious damage if not addressed promptly. Detecting the cause of these leaks and taking immediate action is key to protecting your property. Water seeping into your home can damage walls and floors, and, if left unchecked, can promote mould growth.
Reasons for leaks around a Windowsill:
Typically, leaks around windowsills happen due to:
Failed Caulking or Sealant: Over time, the caulking around your window frame can crack or peel, creating openings where water can enter.
Damaged Flashing: Flashing is the metal material installed around your window to direct water away from the wall. If it becomes damaged or misaligned, it can allow moisture to seep into the window frame and surrounding areas.
Improper Installation: If the window wasn’t properly installed to begin with, gaps can form between the window frame and the wall, allowing water to get in.
Natural Settling and Movement: Over time, your home may shift or settle, especially during changes in temperature. This can cause the window frame or sill to move, creating new gaps and pathways for water.
What’s Happening at the Joint?
When dealing with leaks around a windowsill, the problem often lies at the joints, where different building materials meet. The two most common types of joints involved are expansion joints and construction joints. Here’s a closer look at each:
1. Expansion Joints
Expansion joints are specifically designed to allow for movement in a building. This movement typically occurs due to temperature fluctuations, settling, or shifting of the structure. These joints accommodate the natural expansion and contraction of materials like concrete, brick, or masonry.
- What goes wrong? Over time, the sealant around the expansion joint can degrade, crack, or wear away, leaving gaps where water can seep in. If the joint is improperly sealed from the start, or if the sealant deteriorates, water infiltration can occur, leading to leaks around the windowsill.
2. Construction Joints
Construction joints are formed where two parts of the building come together—such as where the wall meets the windowsill. These joints are critical in ensuring the structure stays intact, but if they’re not sealed correctly, they can be a major entry point for water.
- What goes wrong? If the sealing material at construction joints is applied incorrectly, or if it cracks or degrades over time, water can seep through. The intersection between a wall and a windowsill is particularly vulnerable because it’s a high-stress area where shifting and settling can occur, causing the seal to fail and letting moisture in.
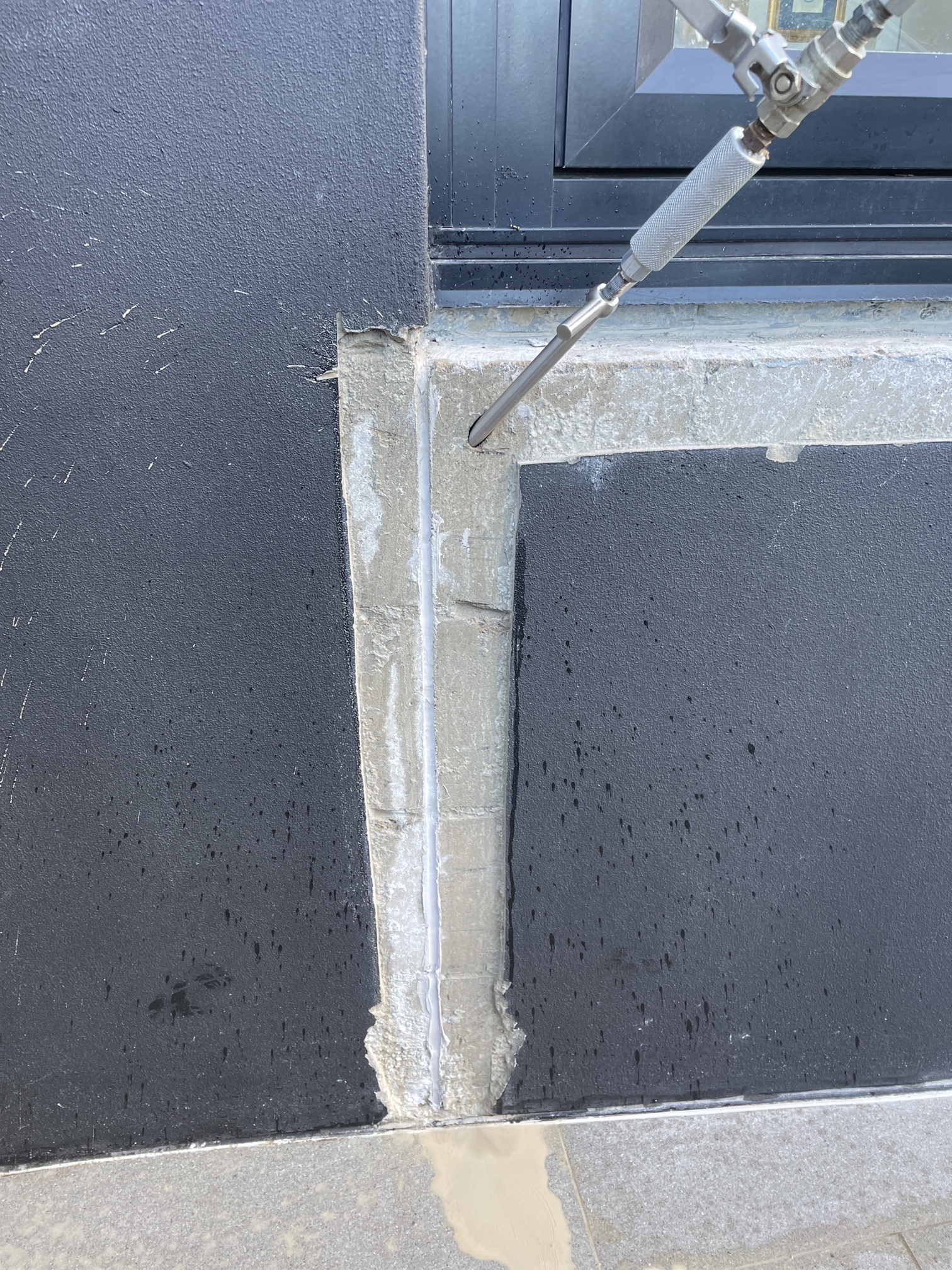
Window Construction Joint
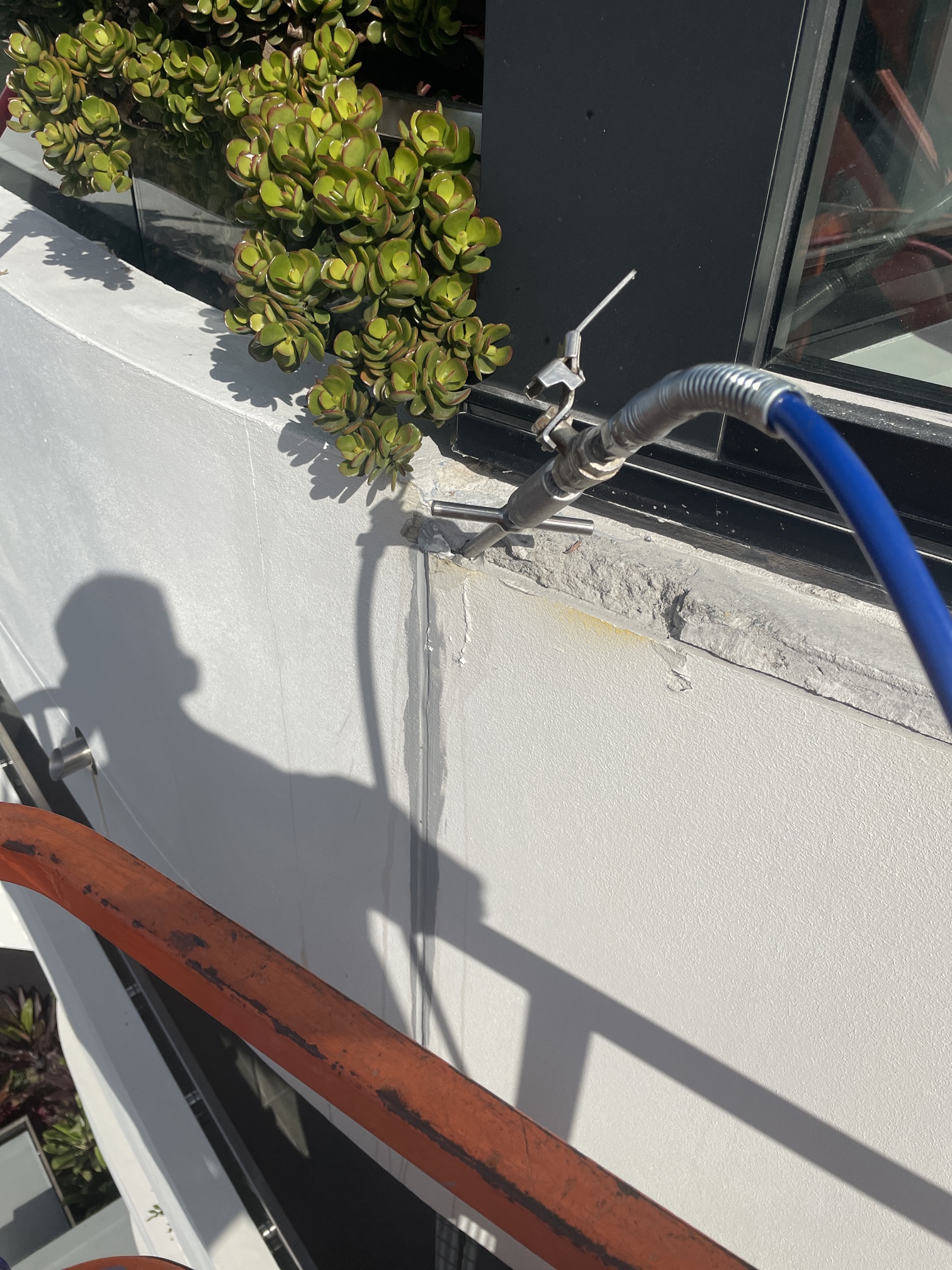
Window Construction Joint
Why SNSeal Injectable Sealant is the Answer
While you could reapply traditional caulking around the window frame, SNSeal Injectable Sealant offers several advantages over standard methods:
1. Targeted, Deep Sealant Injection
Stop & Seal stands out for its ability to penetrate deep into cracks and gaps that are typically difficult to reach with traditional sealants. Unlike regular caulking, which is applied on the surface, Stop & Seal is injected directly into the core of the problem areas, such as deep joints between the window frame and the wall. This ensures a thorough, long-lasting seal even in areas that are otherwise hard to treat, effectively preventing water from seeping in.
2. Precise, Minimal-Disruption Application
The high-pressure injection method allows for extremely precise targeting of the leak source. By using controlled pressure, the sealant is applied exactly where it’s needed, with minimal mess and disturbance to surrounding areas. This makes the process faster and cleaner, avoiding the hassle and inconvenience often associated with traditional caulking methods.
3. Flexible and Durable
Windows are subject to natural movement. As the temperature changes or your home settles, your window frame and sill may expand or contract. Stop & Seal’s rubber-based formula stays flexible after curing, which means it can adjust to these movements without cracking or losing its seal. This ensures long-term protection against leaks.
4. Safe for Indoor Use
Stop & Seal is made from a non-toxic, rubber-based material. This makes it safe for use in areas where you might have pets, children, or sensitive individuals.
Example Project:
Rooftop Podium (Window and Wall Junctions)
The primary concern on this rooftop podium was the failed and delaminated joint sealing at window subsills. Water ingress was evident in areas where the joint sealing has deteriorated, specifically around the window-to-wall connections and window-to-slab joints. Delaminated sealing on the window subsills allowed water to penetrate the building structure, as indicated by thermal imaging that showed moisture present in the walls and below tiled areas.
Scope and Methodology:
- Rectify failed window subsill sealing along with perimeter wall-to-slab joints and wall-to-column joints.
- Use SNSeal high-pressure injectable sealant to re-seal the areas where water has infiltrated, particularly at window-to-wall joints.
- Access for this work was provided via high ropes access team for hard-to-reach façade areas.
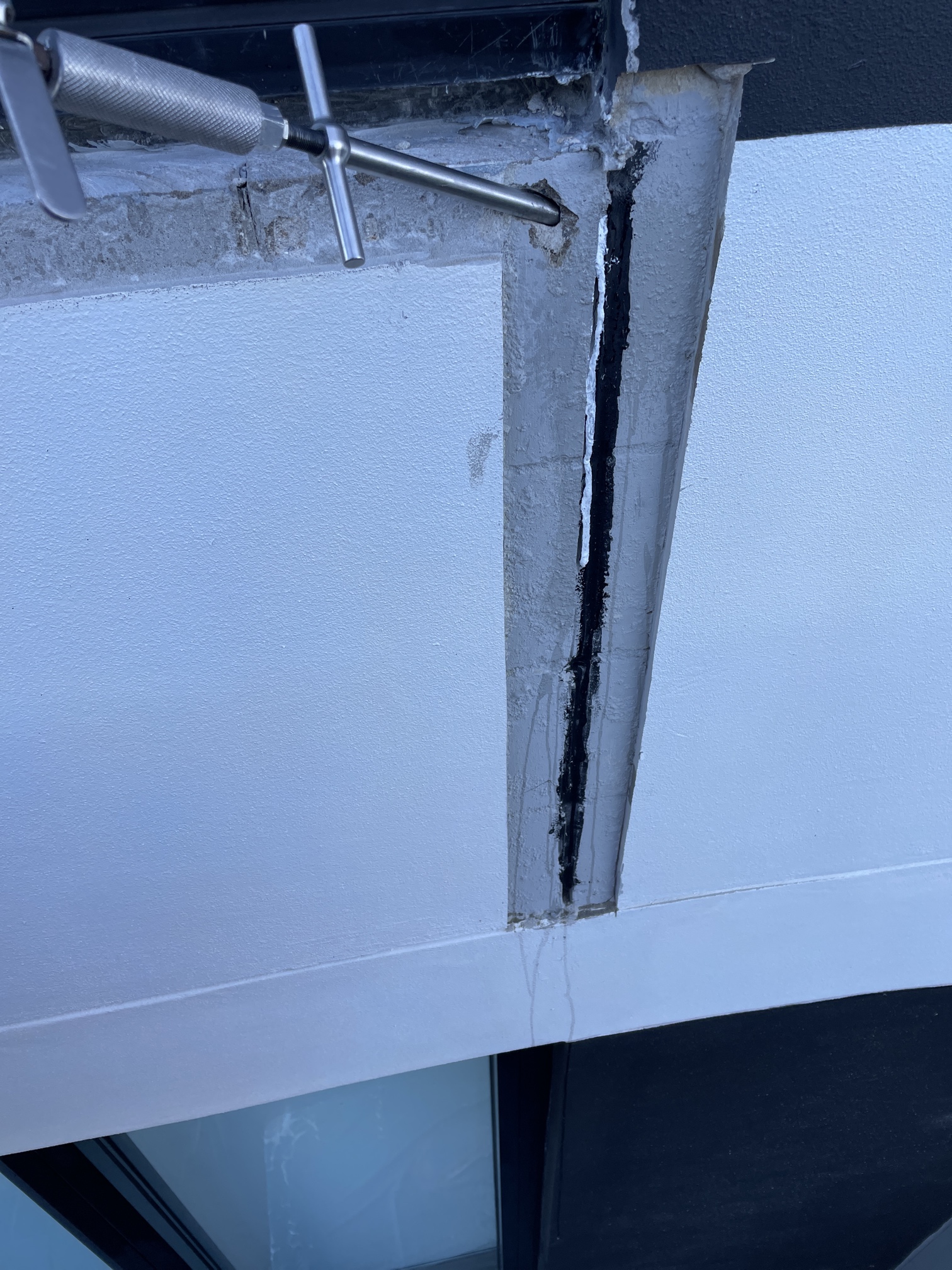
Window Construction Joint
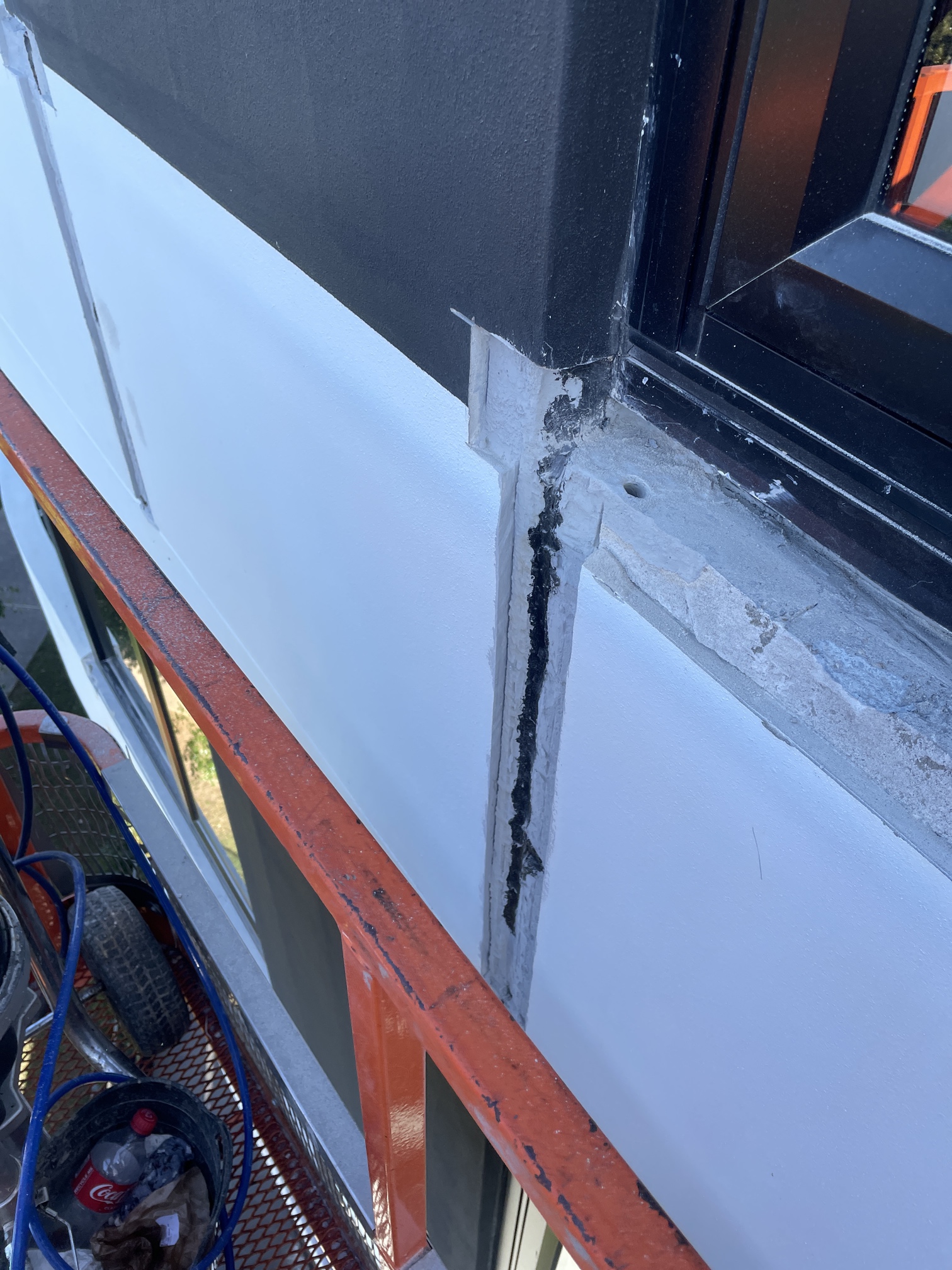
Window Construction Joint
If you’re dealing with water ingress around your windows, don’t wait contact us today, and let us show you how our Stop & Seal solution can keep your building safe from water intrusion.