Our team was called to a project in Caloundra, Queensland where concrete cancer and blowout corrosion were discovered beneath the rooftop membrane system, issues that were also contributing to serious water ingress and mould growth in the top-floor apartment. What began as a moisture problem turned into a full-scale structural and waterproofing repair, highlighting the importance of early detection and quality remediation. This blog outlines how we delivered a complete solution through expert concrete cancer repair and rooftop membrane waterproofing.
The Problem: Concrete Cancer & Water Ingress
We started inside the top-floor apartment, where the tenant had reported persistent mould. A closer look at the ceiling revealed several fine cracks, which are clear signs that water had been making its way in from above. These weren’t just surface blemishes; they were active pathways for moisture, feeding mould growth and creating an unhealthy living environment.
From there, we moved up to the rooftop to trace the source. As we removed the perimeter flashings, the real issue became clear, concrete cancer was silently spreading beneath. The reinforcing steel (reo bar) embedded in the concrete had begun to corrode, expanding and causing the concrete to crack and break away. Left untreated, this kind of damage can seriously compromise a building’s structural integrity. It was clear we needed to act fast to stop further deterioration and restore proper waterproofing protection.
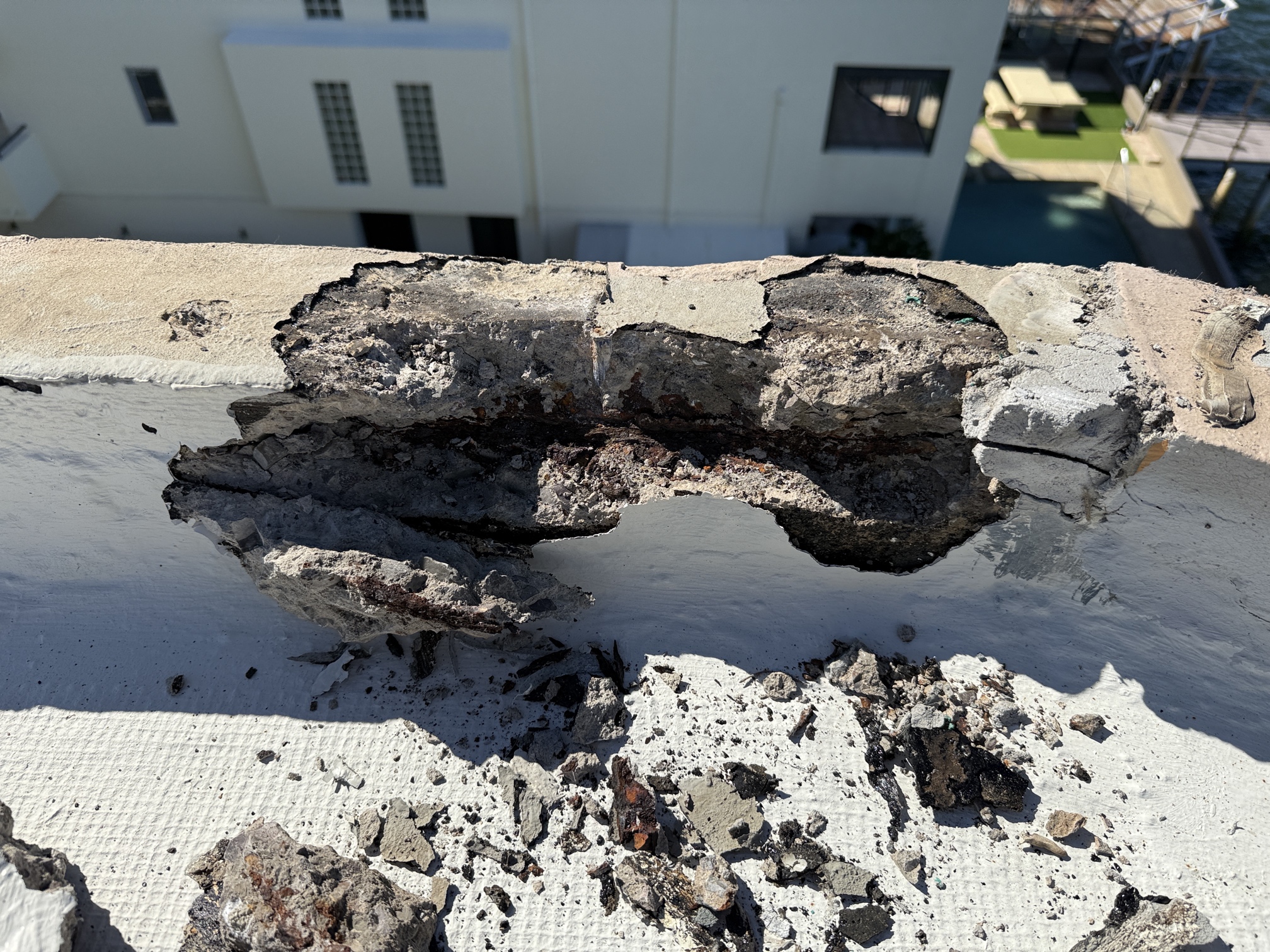
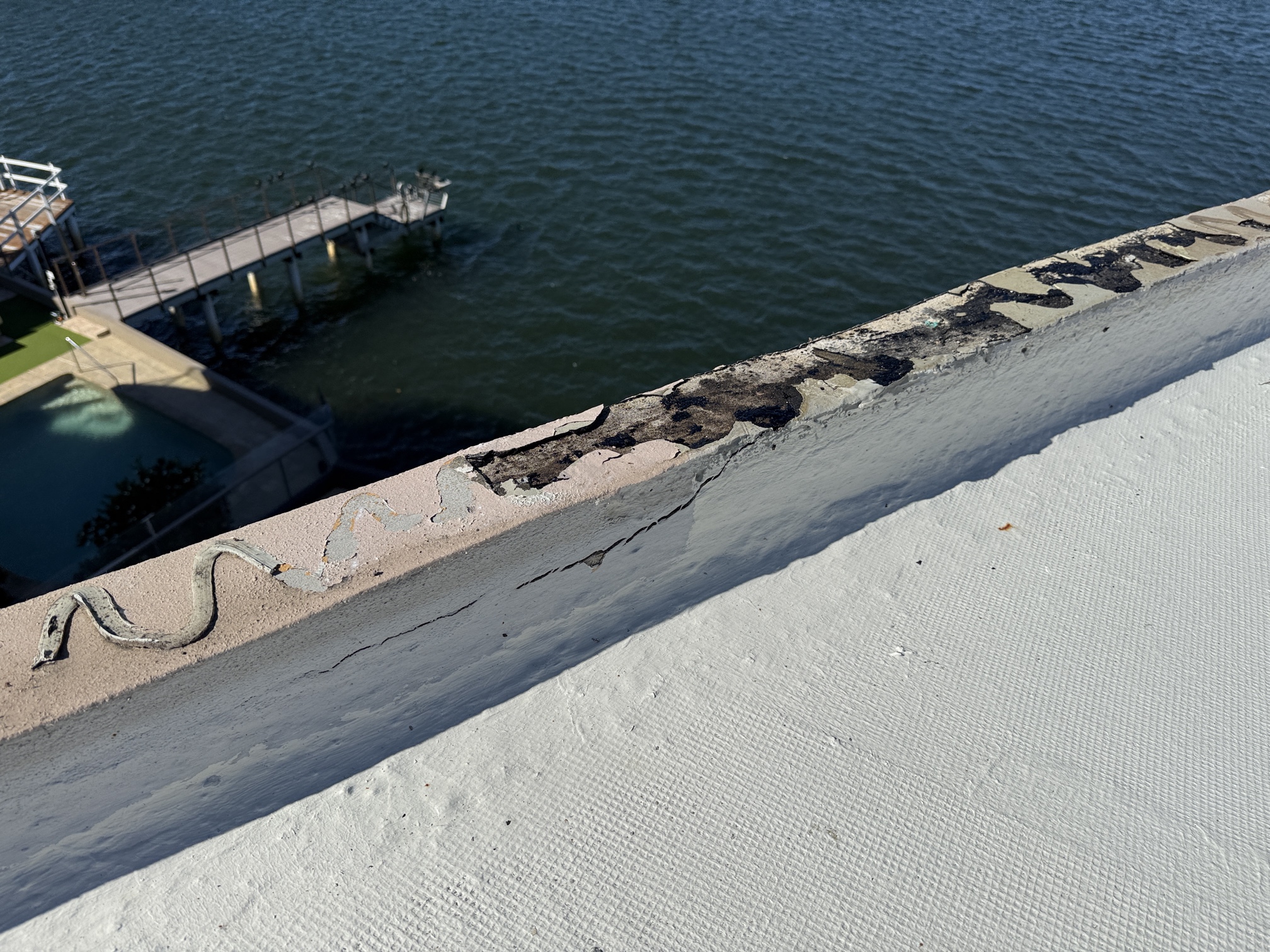
Our Solution: A Comprehensive Approach
We provided a detailed scope of works, divided into three main sections to address both the internal and external issues:
Scope of Works 1: Internal Ceiling Injection Works
Scope of Works 2: Rooftop Membrane Repair & Concrete Cancer Remediation
Scope of Works 3: Full Rooftop Membrane Reinstallation
Scope of Works 1: Internal Ceiling Injection Works
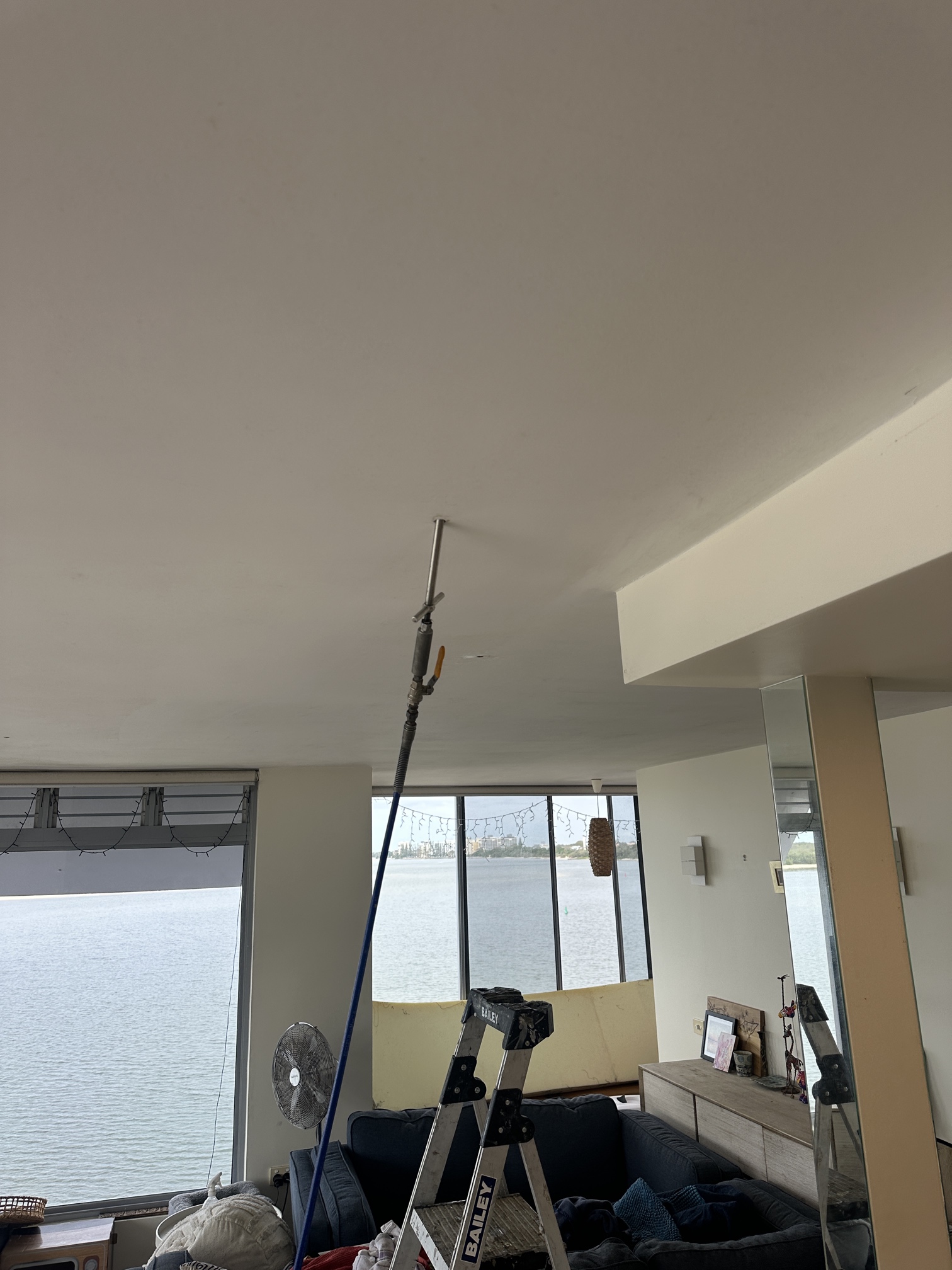
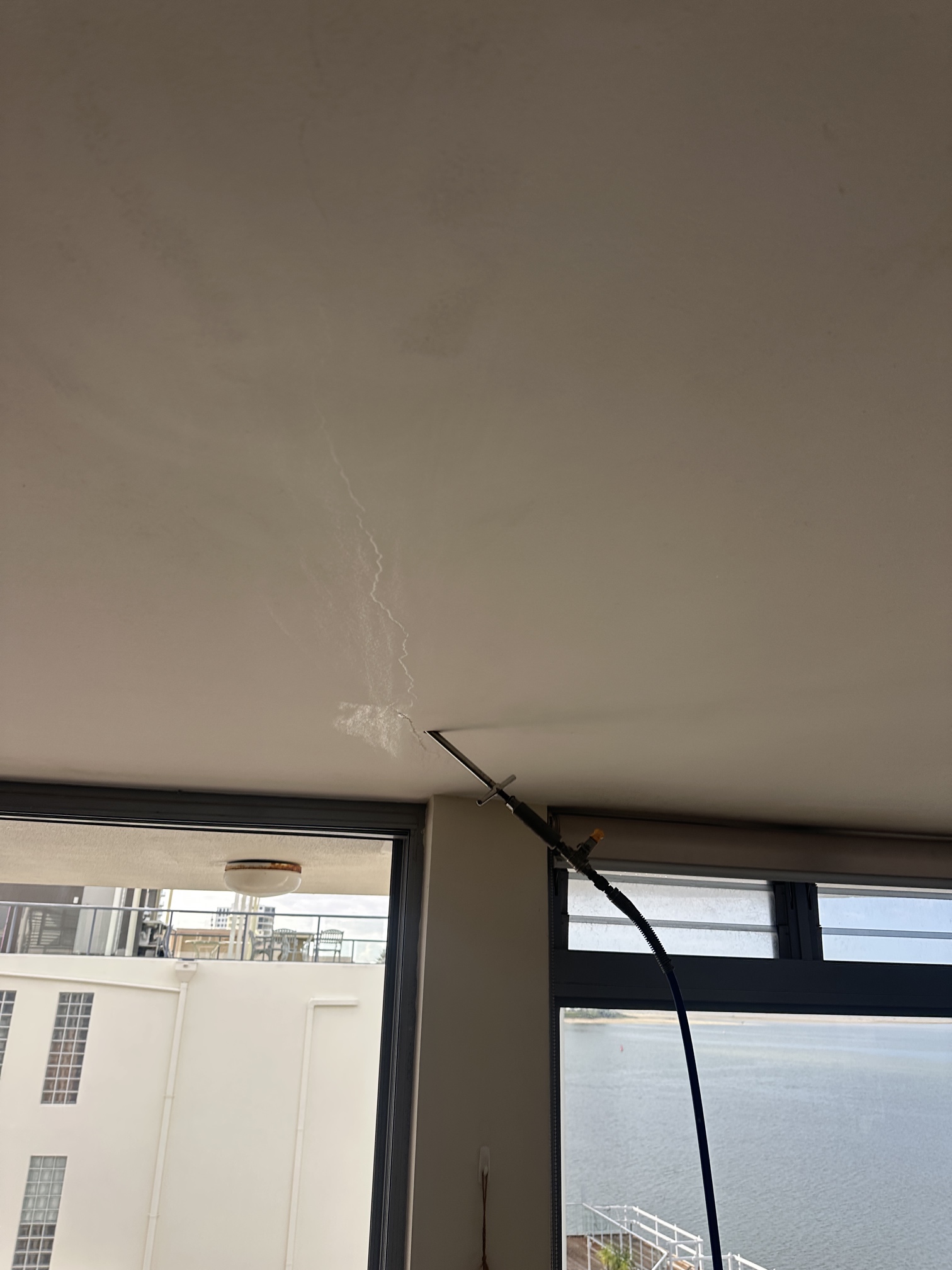
The first step was to inject the cracks in the apartment ceiling with SNSeal high-pressure injectable sealant to form a water-tight seal. The process involved:
- Drilling diameter holes in the ceiling to prepare for injection.
- Injecting SNSeal high-pressure injectable sealant into the cracks.
- Activating the injectable sealant with SNSeal activator.
Scope of Works 2:
Rooftop Membrane Repair & Concrete Cancer Remediation
Once the interior issues were stabilised, our attention turned to the rooftop directly above the affected apartment—specifically over Unit 15, where the water ingress had originated.
We started by stripping back, removing perimeter flashings and grinding off the aged netted membrane to expose the bare rooftop substrate.
That’s when we uncovered a more serious issue: concrete cancer hidden beneath the flashings and along the perimeter, as well as blowout damage at the expansion joint.
1. Perimeter Flashing & Concrete Cancer Remediation:
Upon inspection
We discovered the perimeter flashings were in place, but there was clear evidence of water ingress, mould growth, and areas that had not been adequately membraned. These issues pointed to the need for further inspection and remediation.
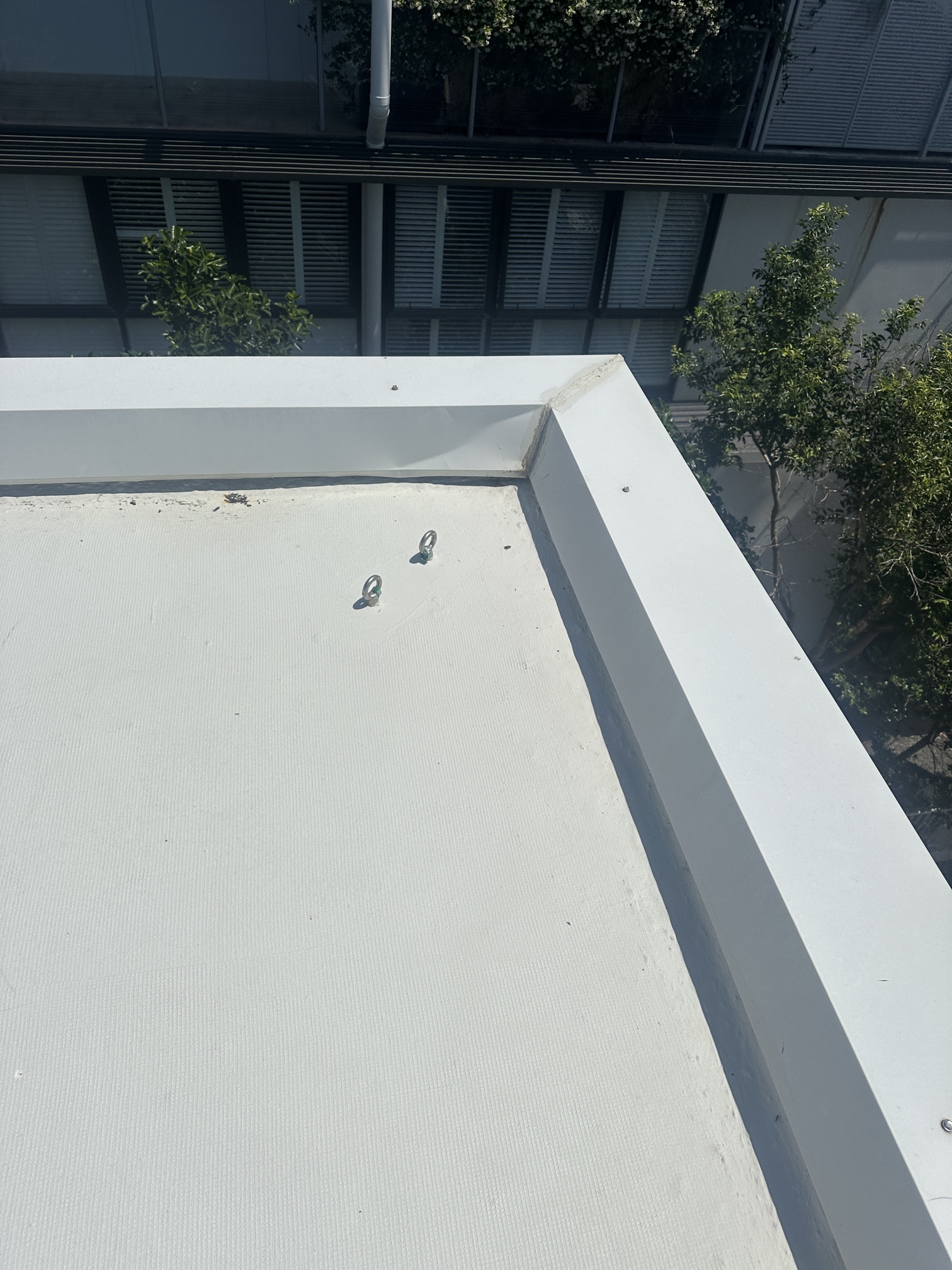
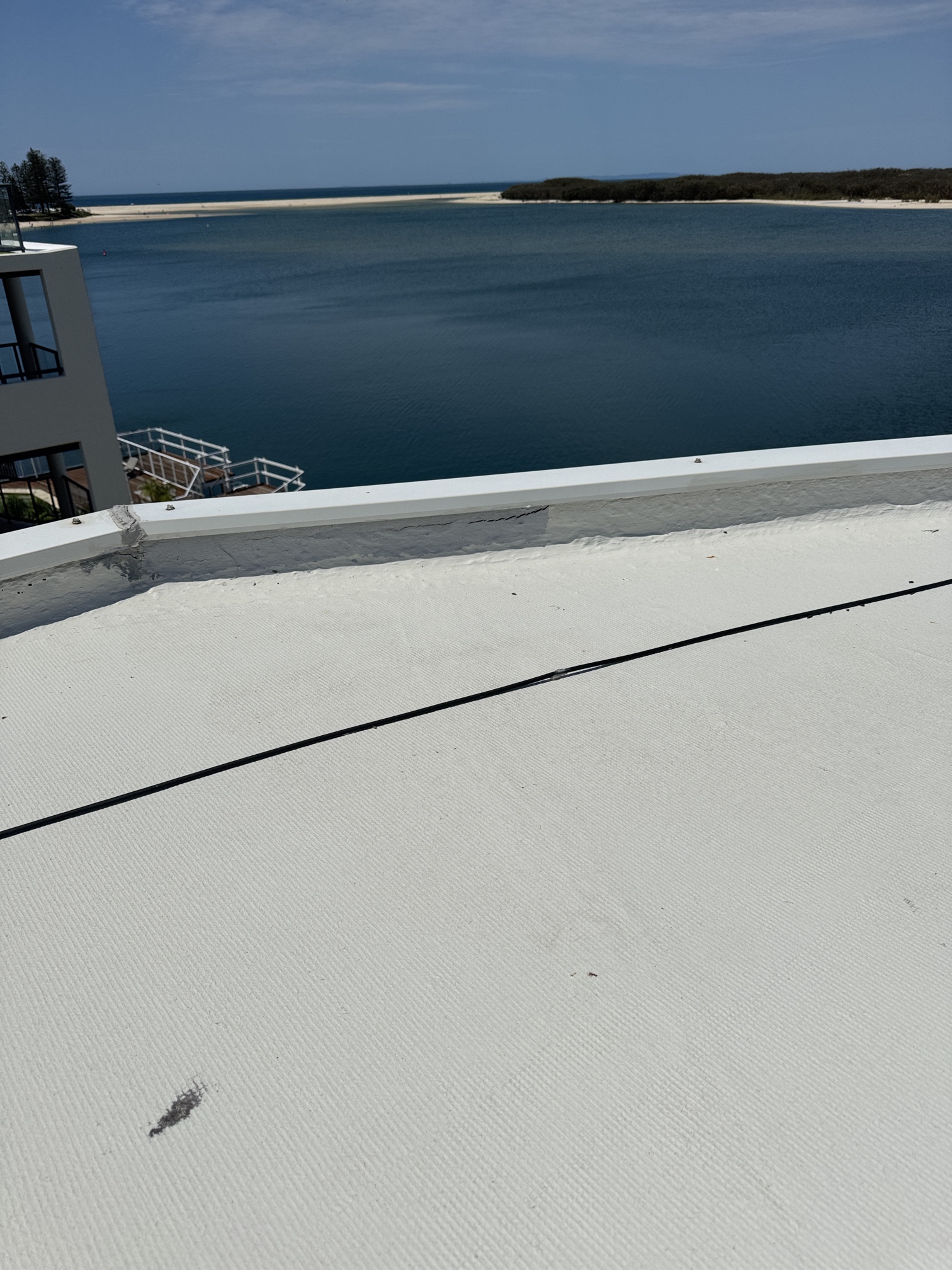
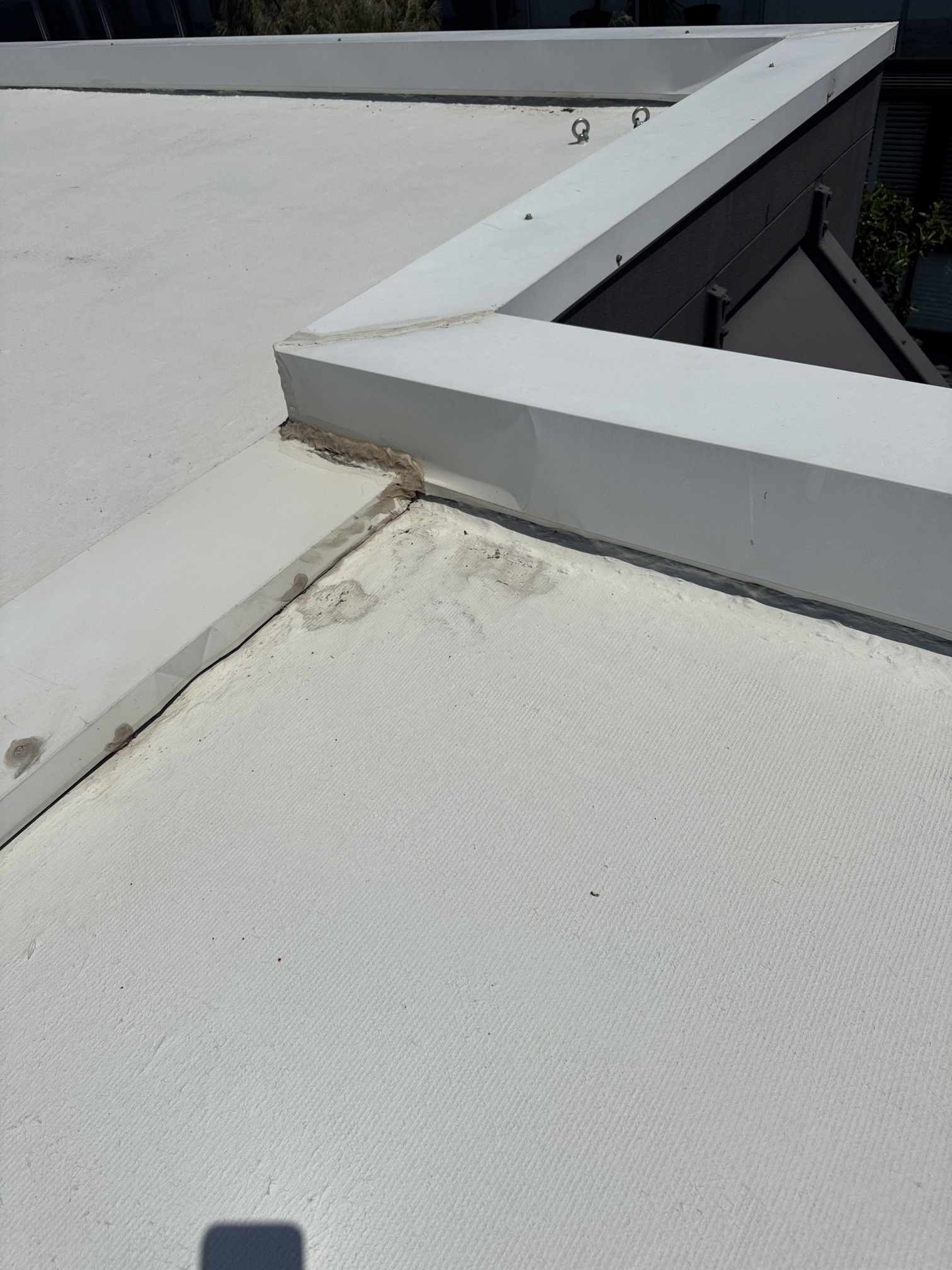
Inspection After Flashing Removal
Once the perimeter flashings were removed from the rooftop upturns, we revealed significant concrete cancer beneath. The corroded steel reinforcement (reo bar) was exposed, and the surrounding concrete had deteriorated, compromising the structural integrity.
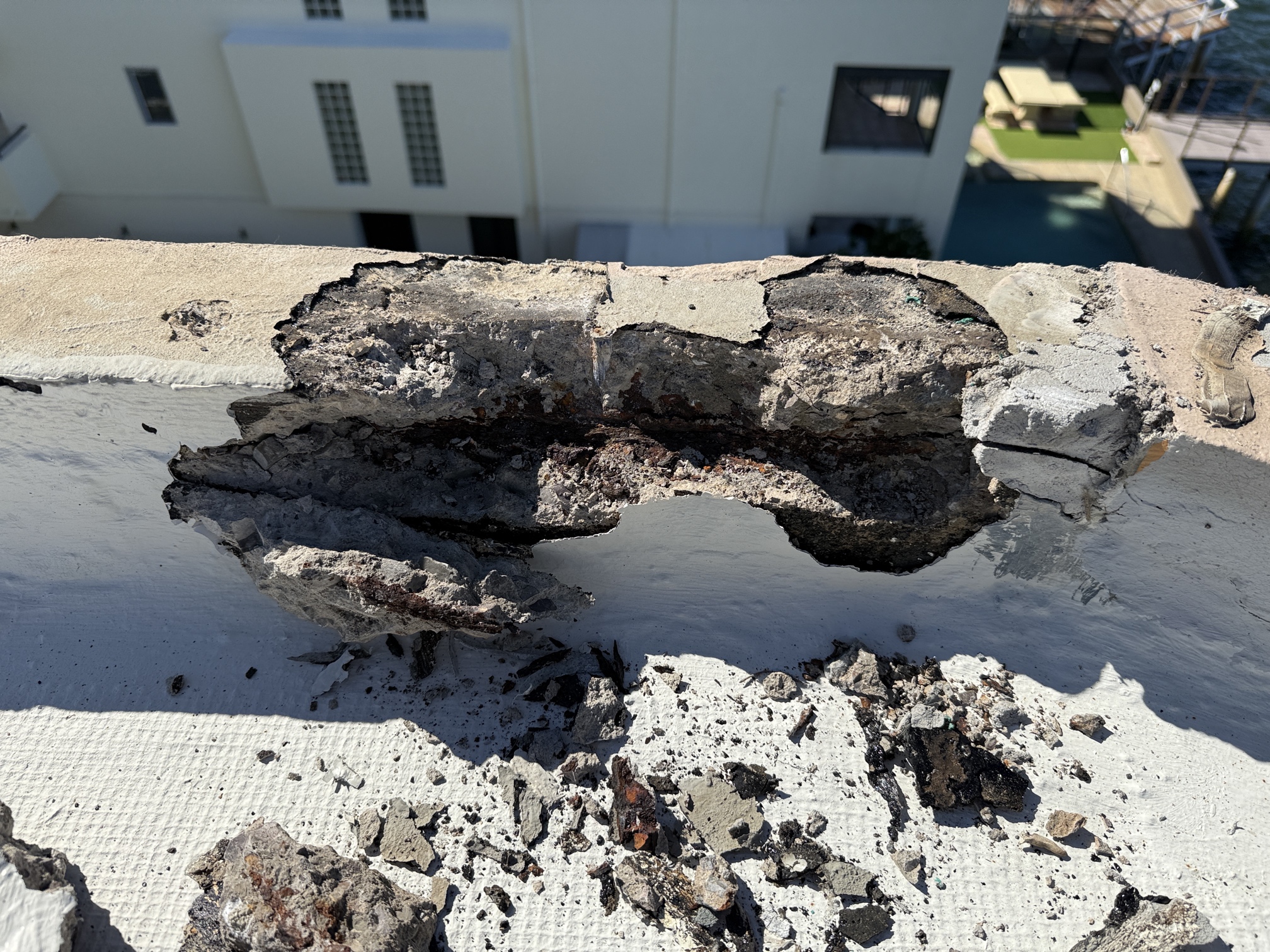
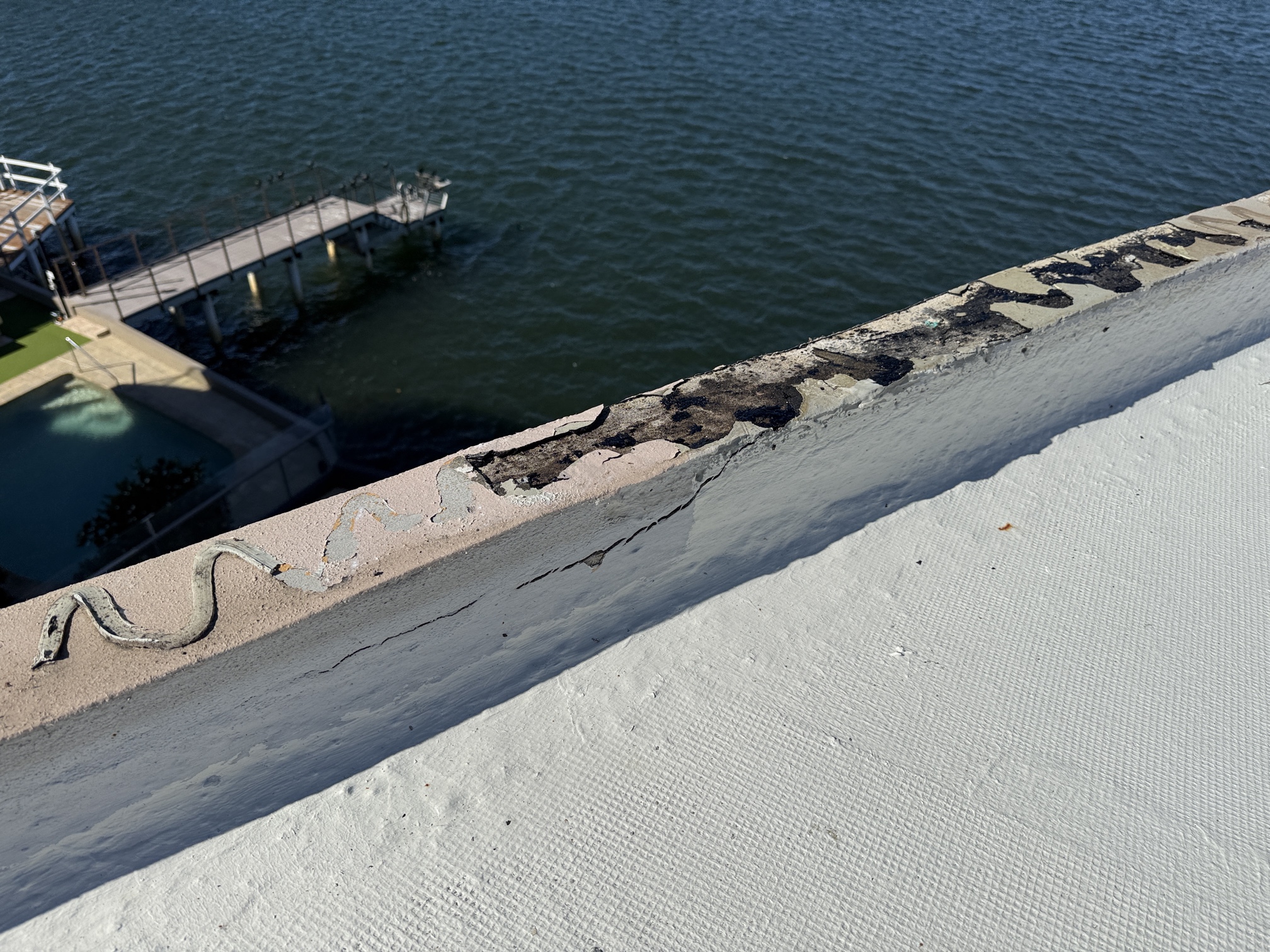
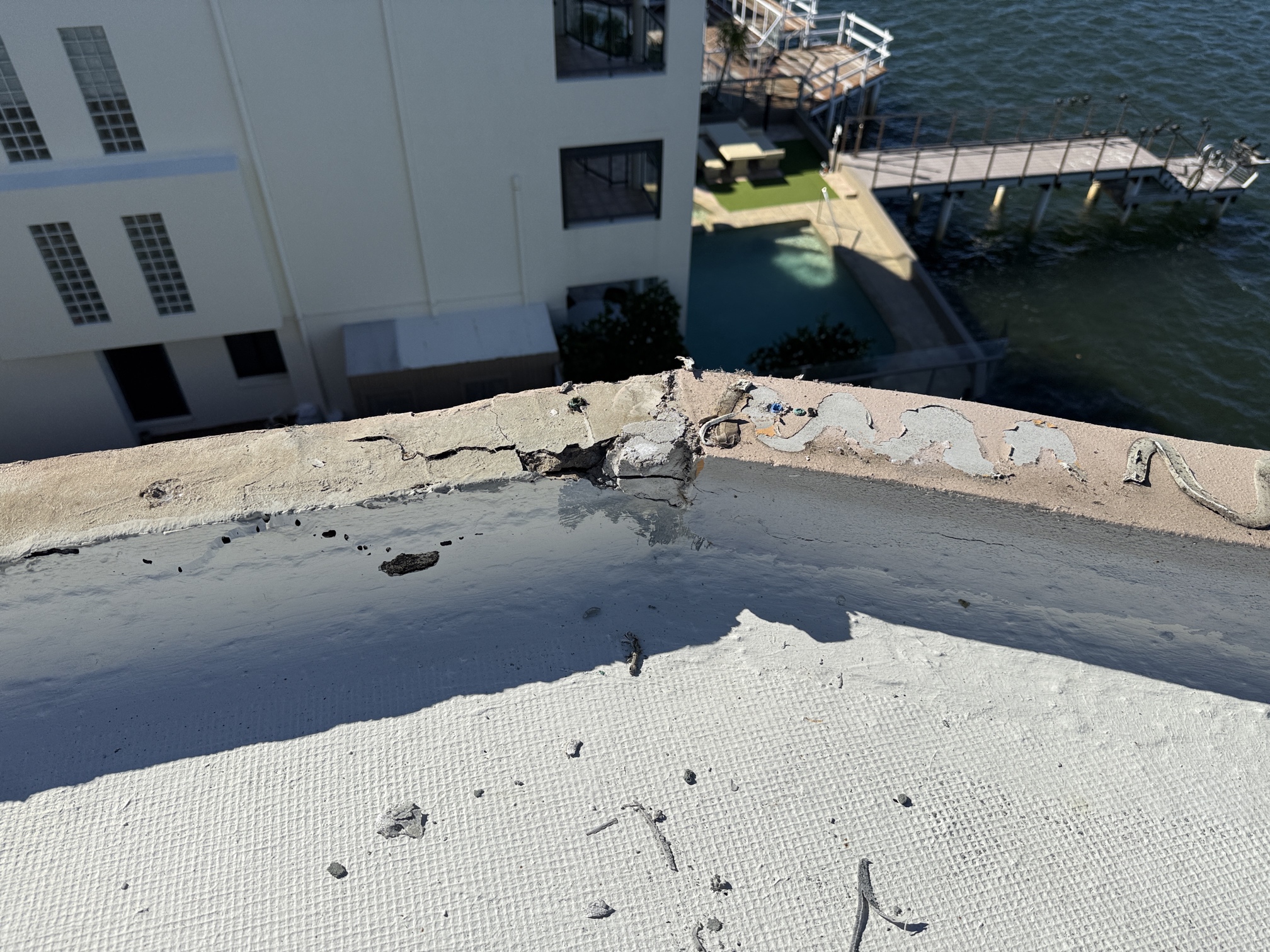
Remediation Steps:
-
-
Jackhammered back the damaged concrete around the perimeter edges to remove the affected areas.
-
Exposed and cleaned the corroded steel reinforcement (reo bar), ensuring it was free from debris and contaminants.
-
Mapped out all areas affected by concrete cancer to ensure comprehensive remediation.
-
Rebuilt the damaged sections using T40 grout to restore structural integrity.
-
Applied a primer coat in preparation for the waterproof membrane installation.
-
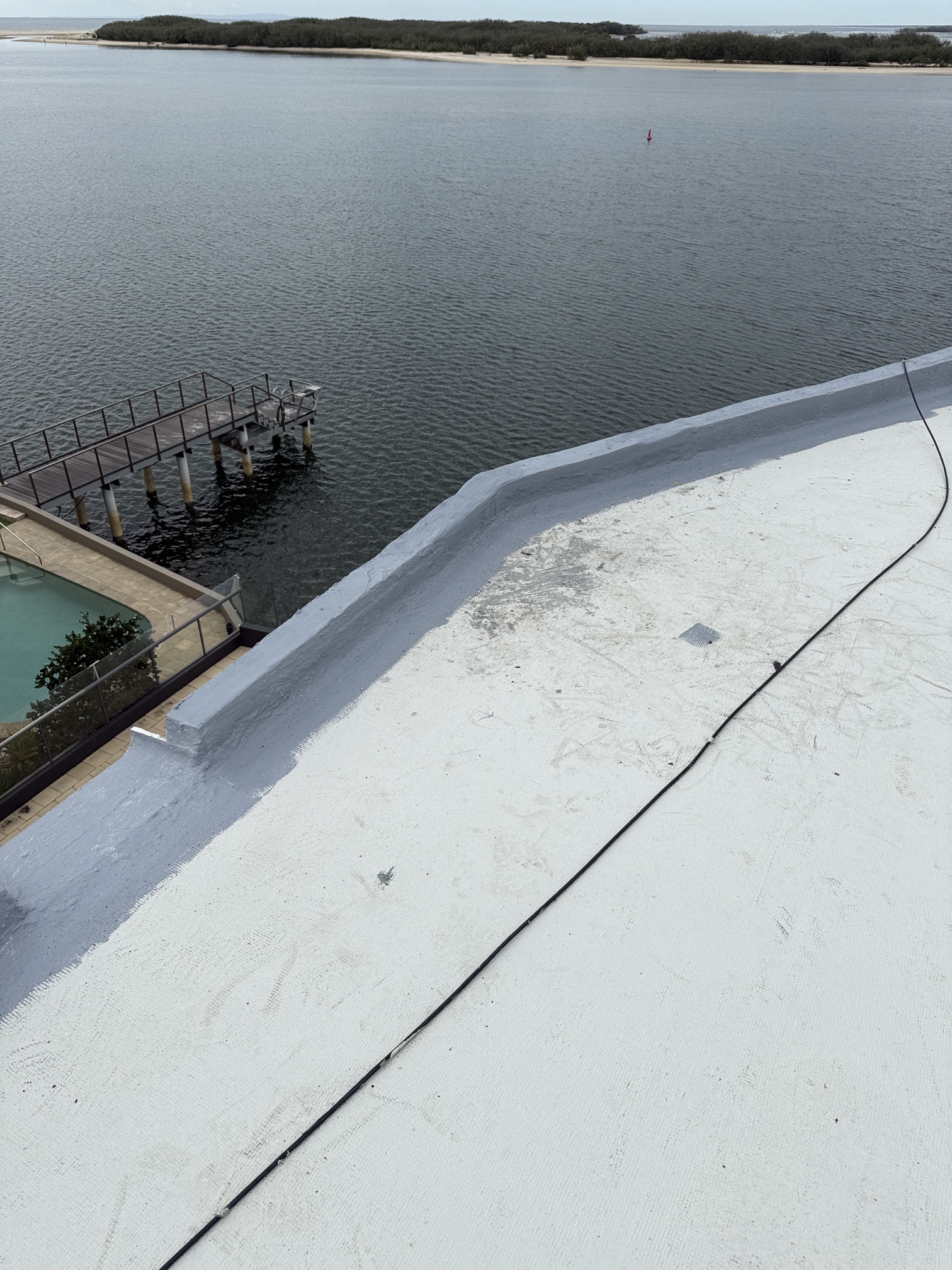
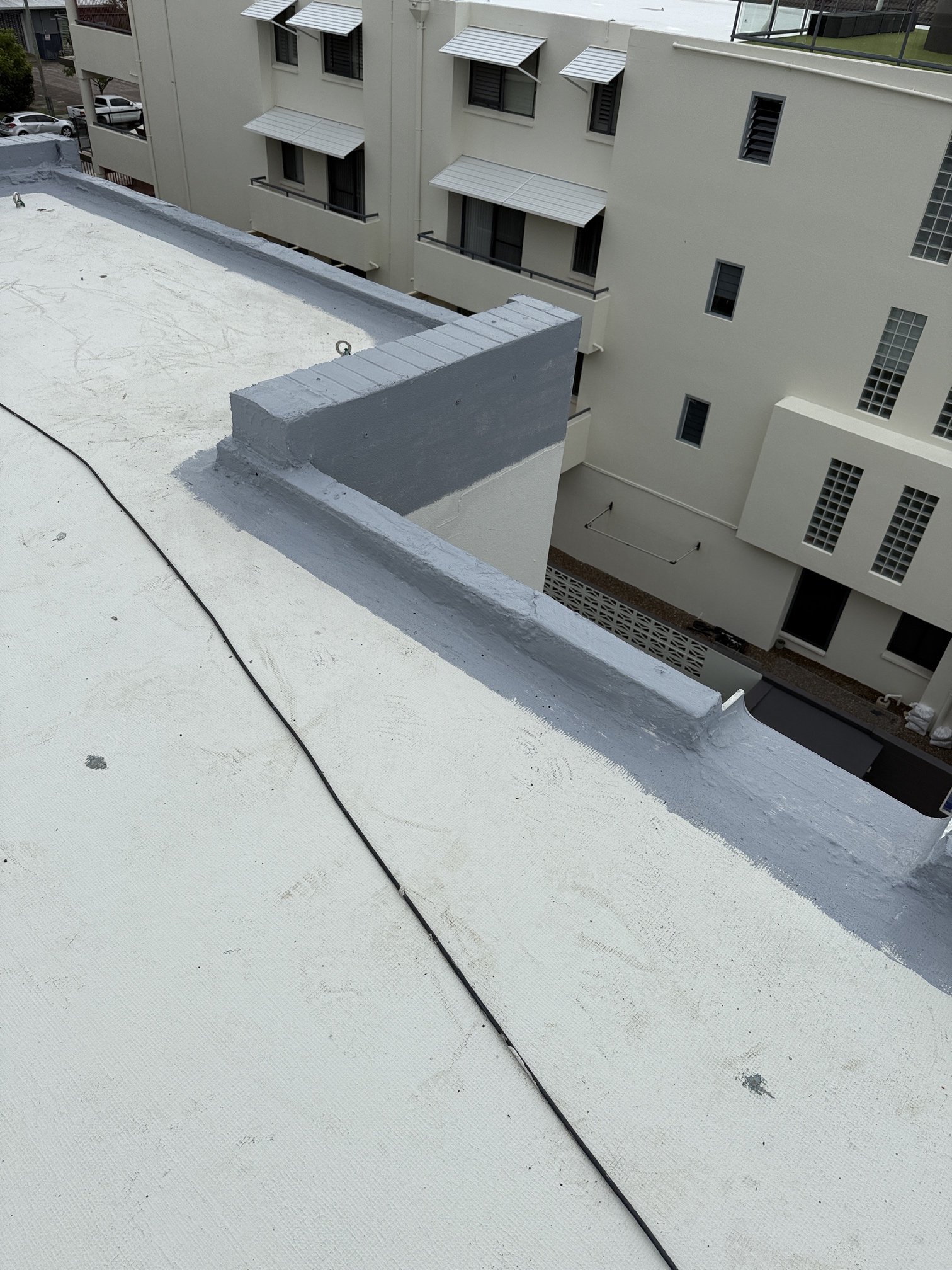
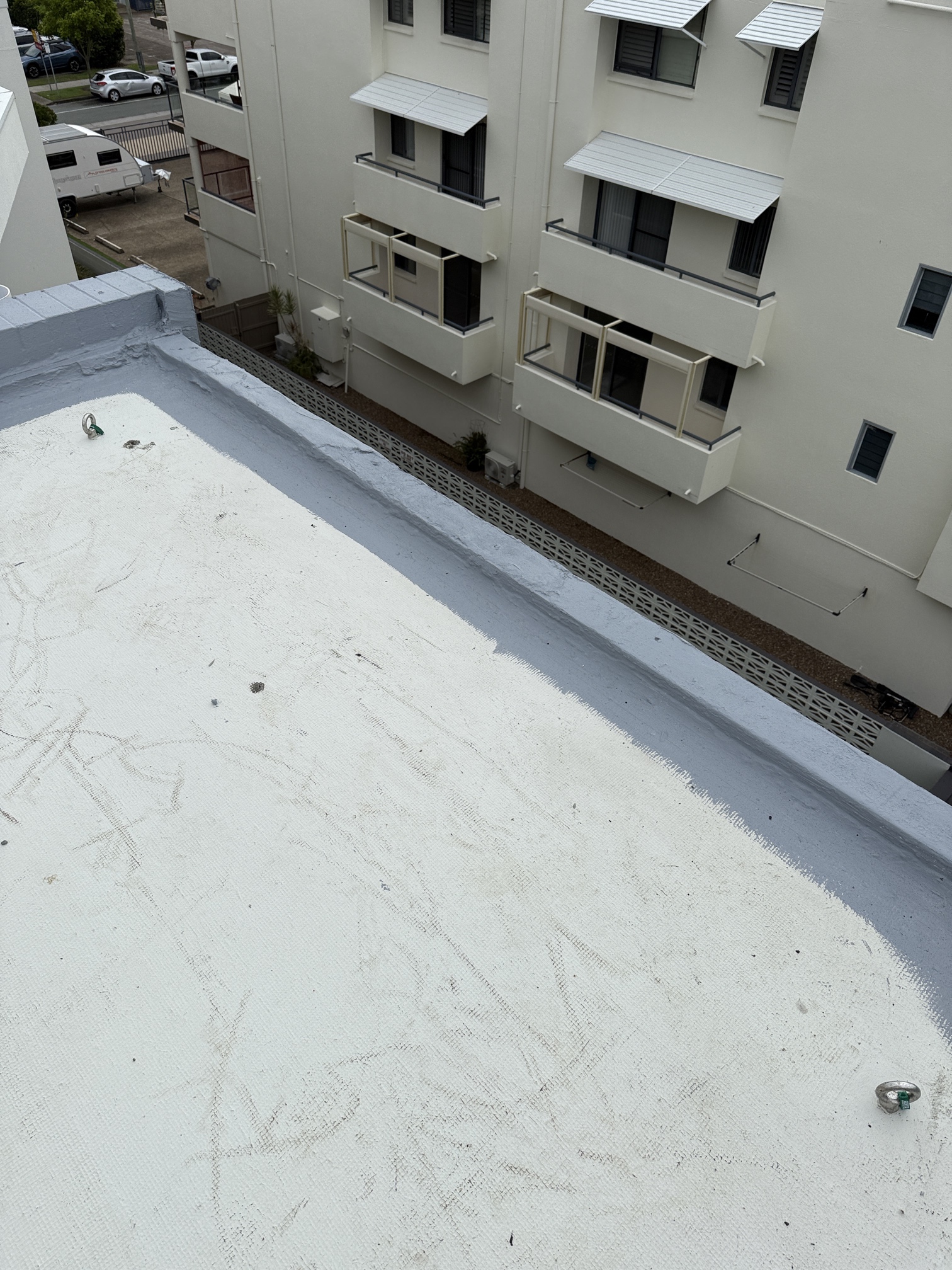
2. Expansion Joint Repair: Concrete Cancer & Blowout Remediation:
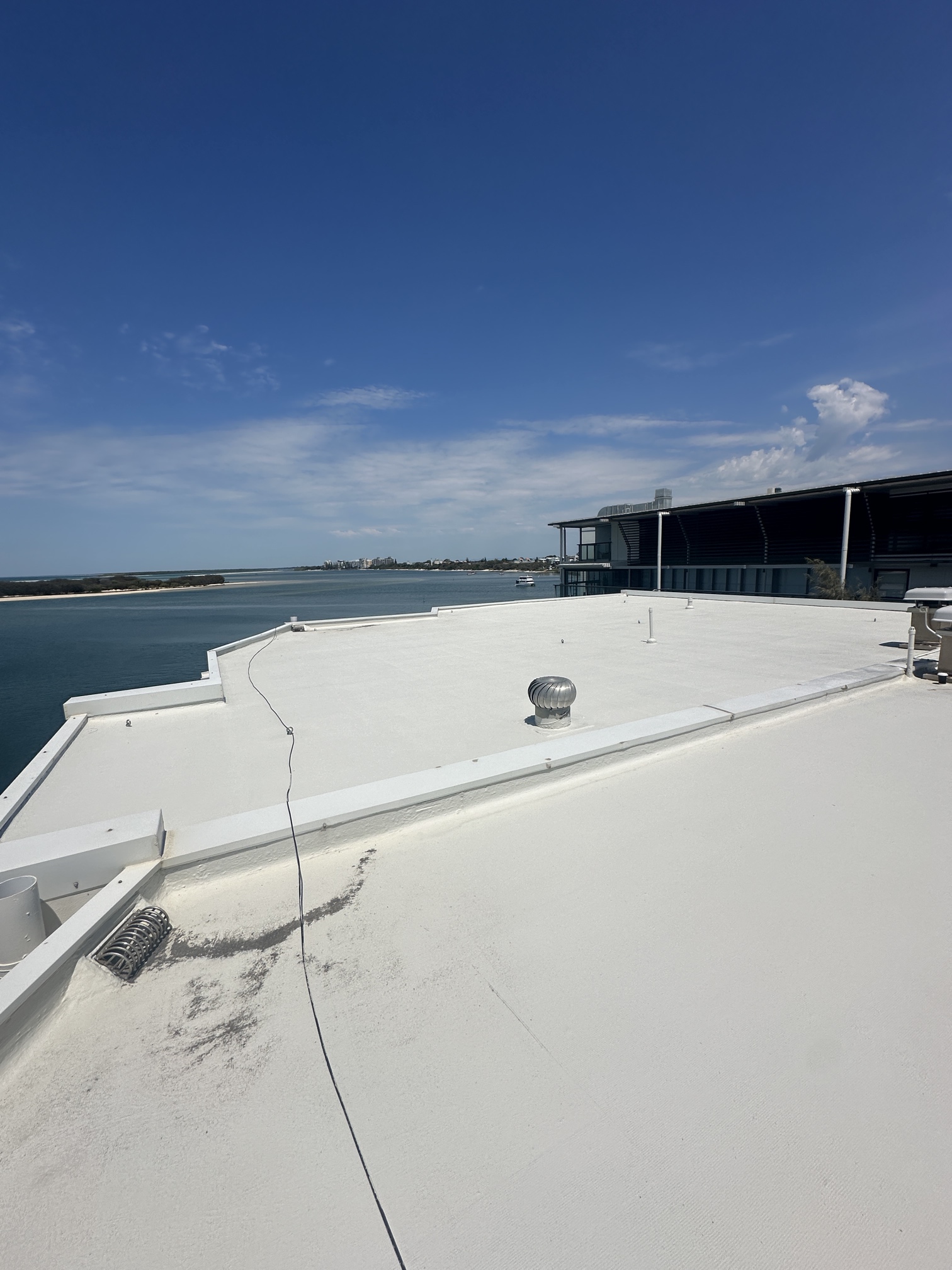
Upon Inspection
The steel hob covering the expansion joint was concealing extensive blowout and advanced concrete cancer
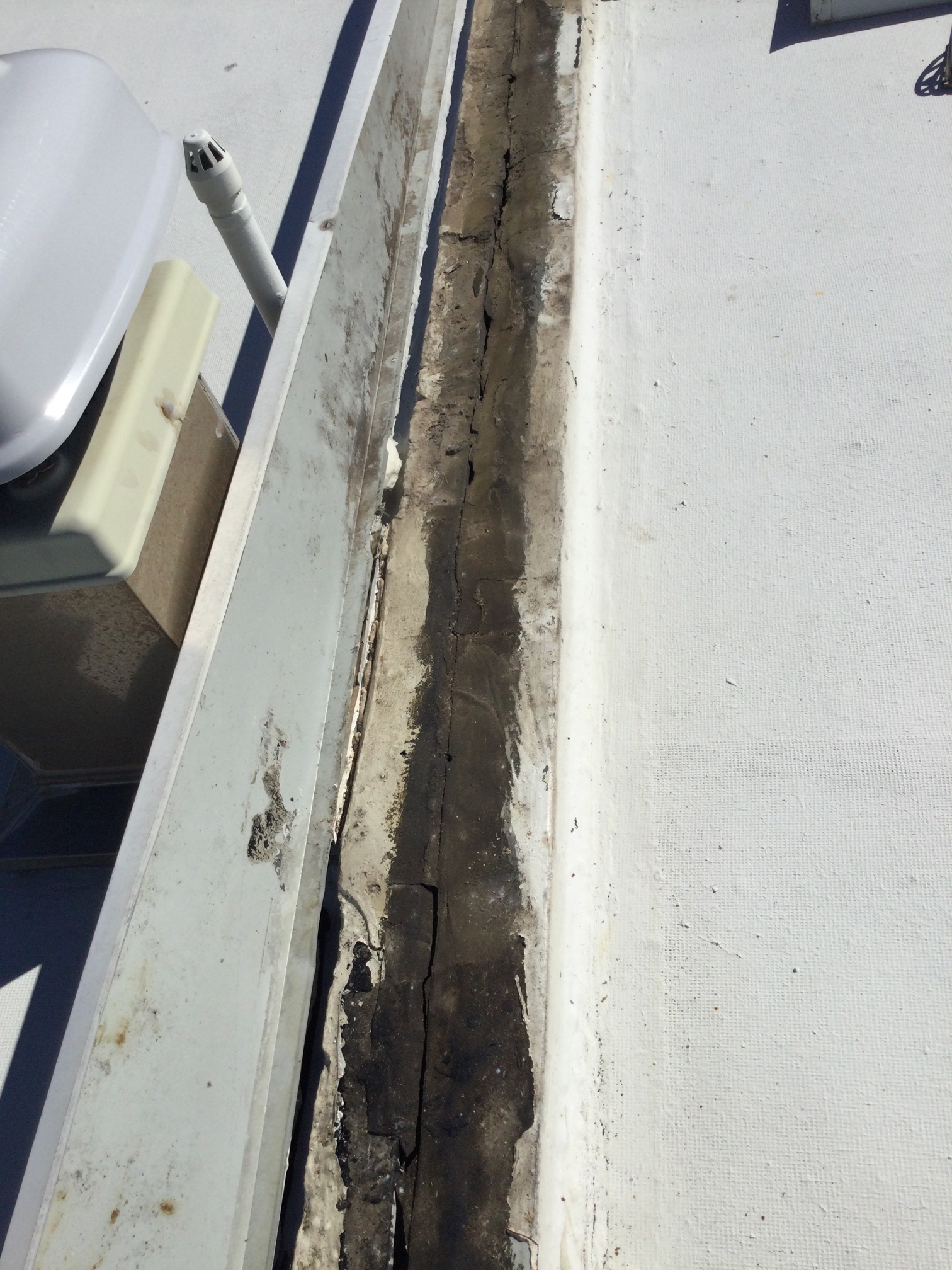
Hob Removal
Removed the steel hob to access the full extent of the damage.
Jackhammered back the deteriorated concrete to expose the corroded reo bar.
Cleaned and mapped the exposed reo to identify all affected areas
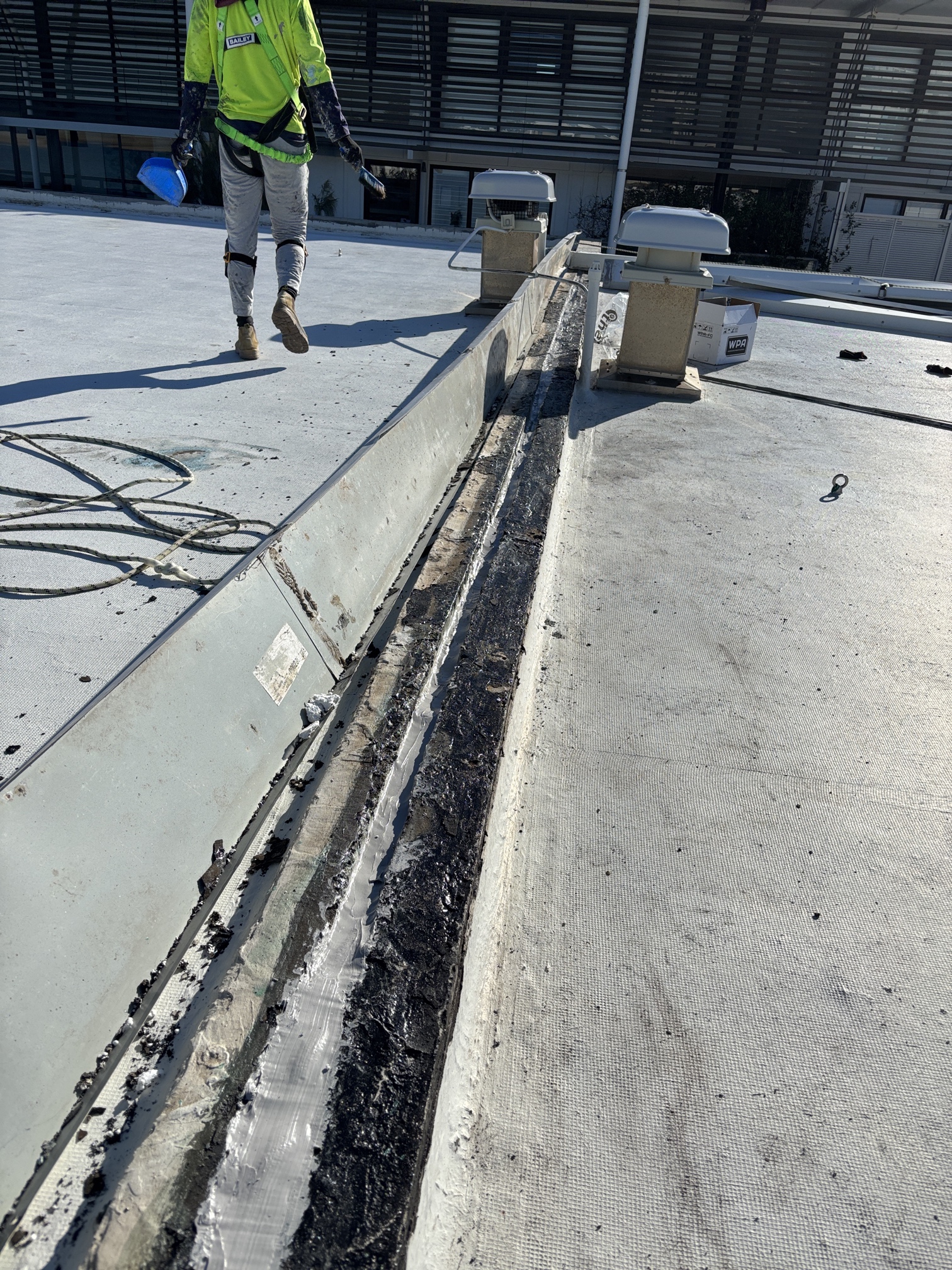
Structural Rebuild
Rebuilt the damaged section using T40 grout to restore strength and stability.
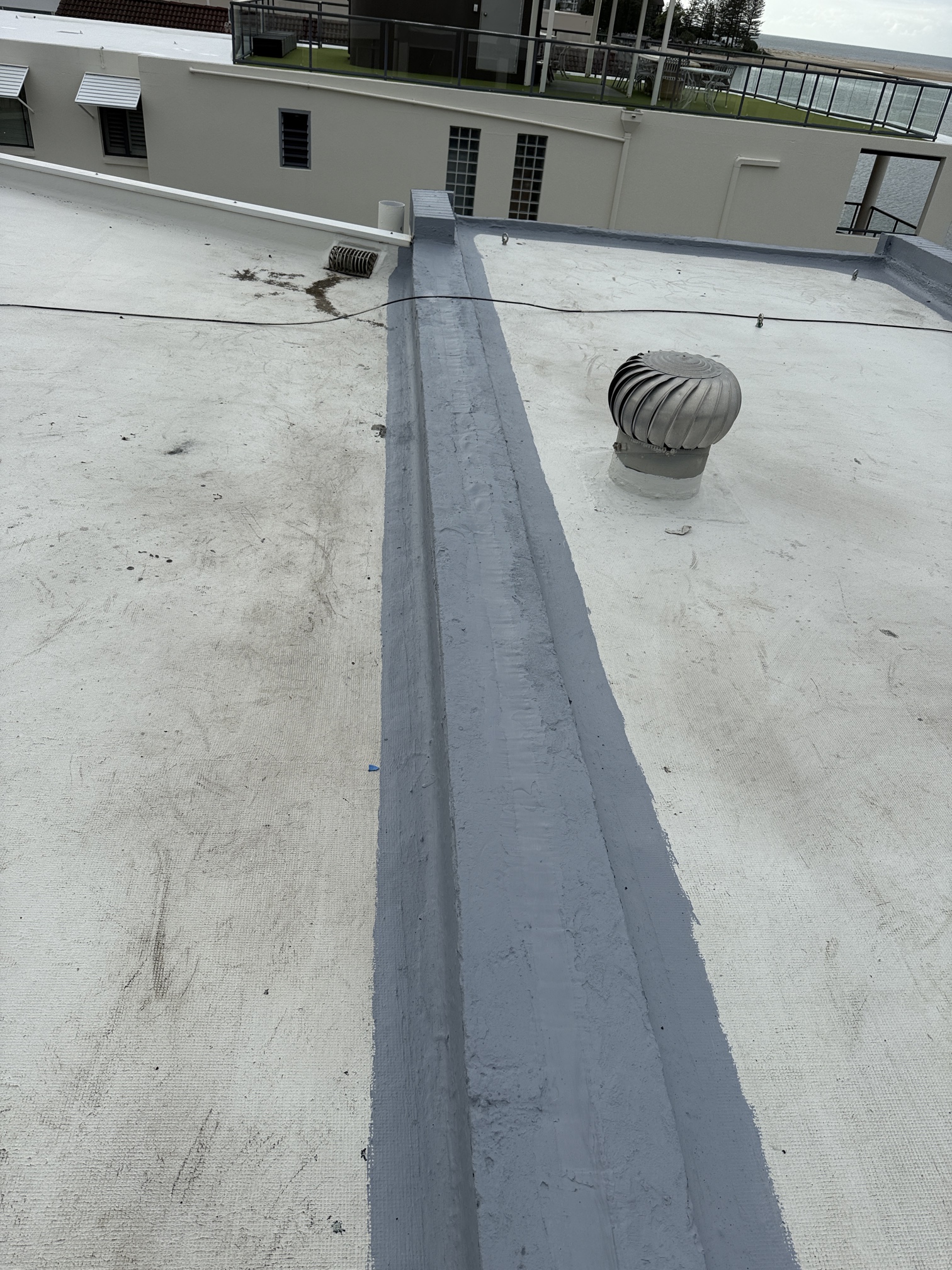
Application
Applied Primer over the hob to prepare for membrane application.
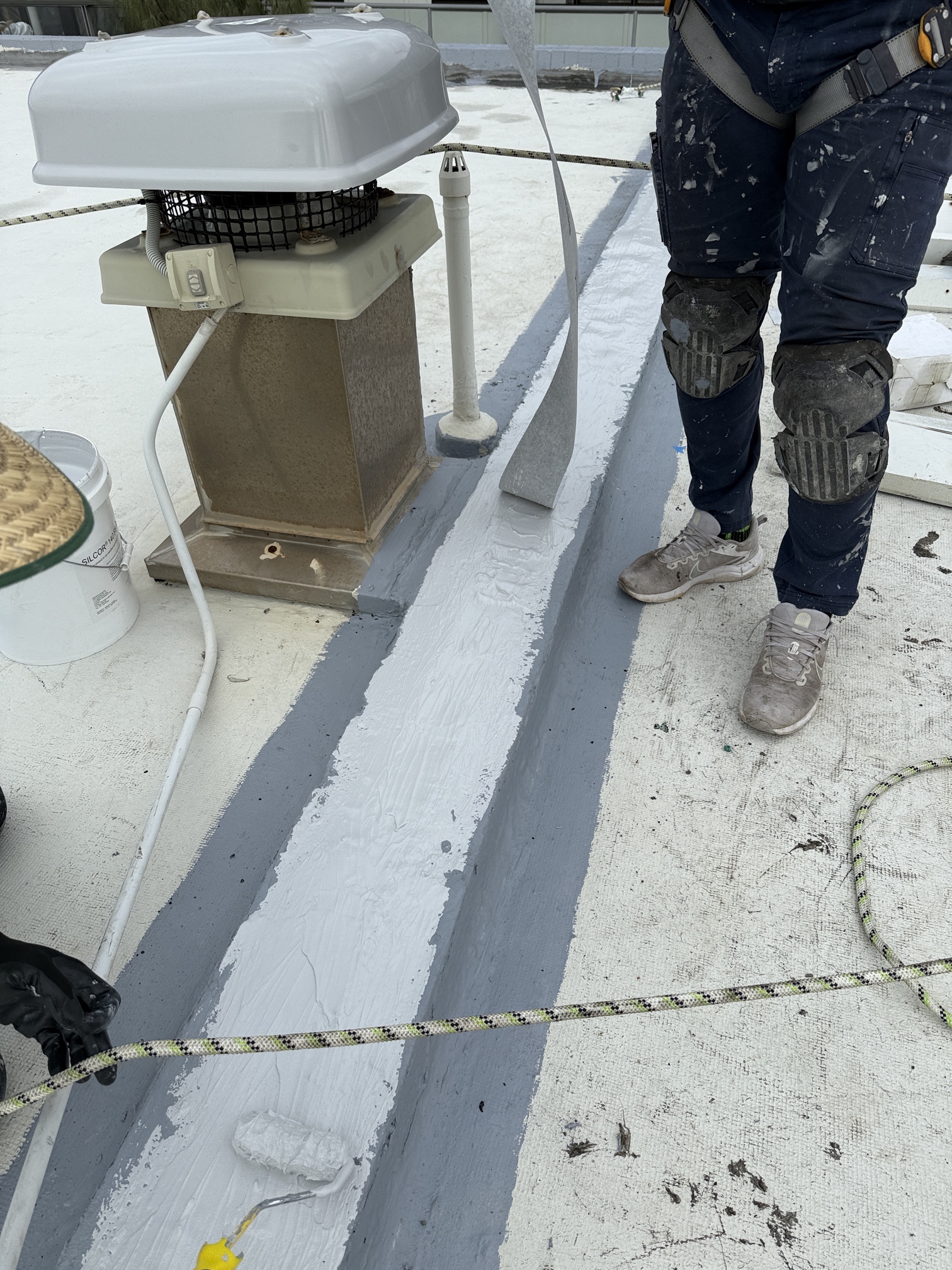
Application
Applied a flexible bandage and waterproof membrane to seal and protect the joint.
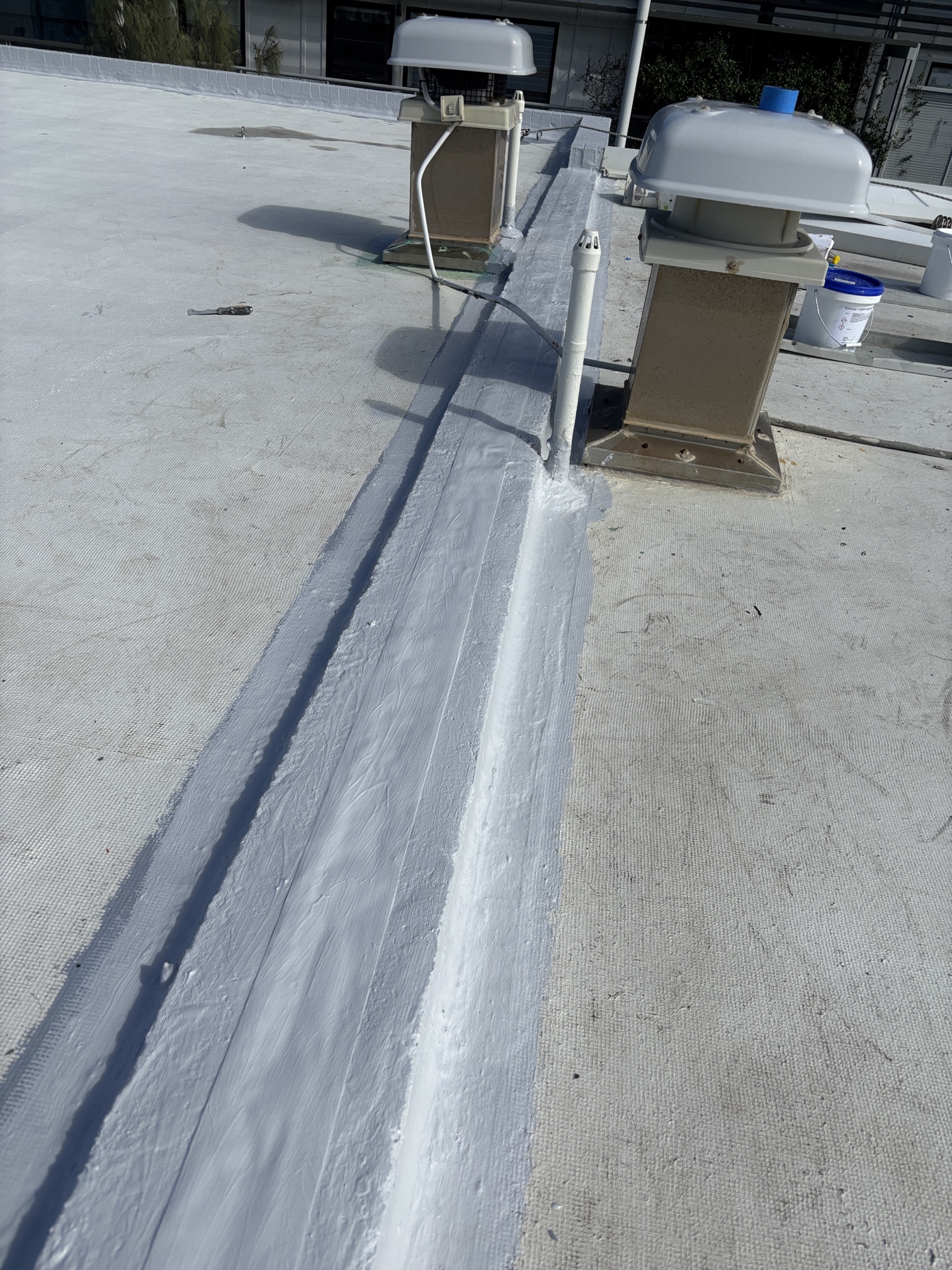
Apply Membrane
Applied Membrane over flexible bandage for added water ingress protection.
Scope of Works 3: Full Rooftop Membrane Reinstallation
After completing the concrete cancer remediation and expansion joint repairs, we moved forward with reapplying the waterproofing membrane across the entire rooftop. This critical step ensured lasting protection from water ingress and reinforced the structural integrity of the building:
-
- Reactivated the existing membrane system to ensure proper adhesion.
- Applied a fresh layer of membrane across the entire rooftop surface.
- Added two coats of Silcor 75 UV stable topcoat for enhanced durability and protection against the elements, up and over the edges of the rooftop area.
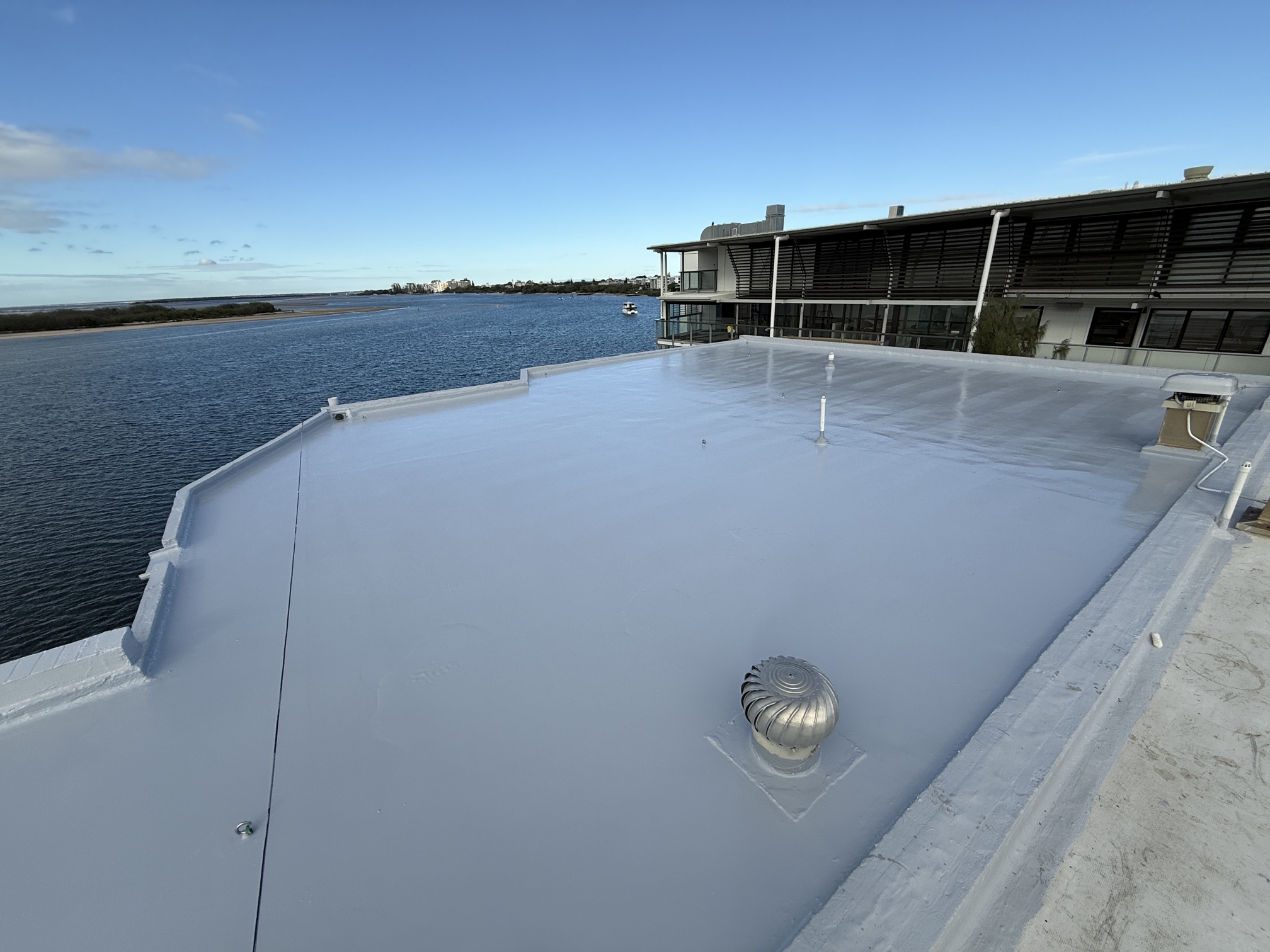
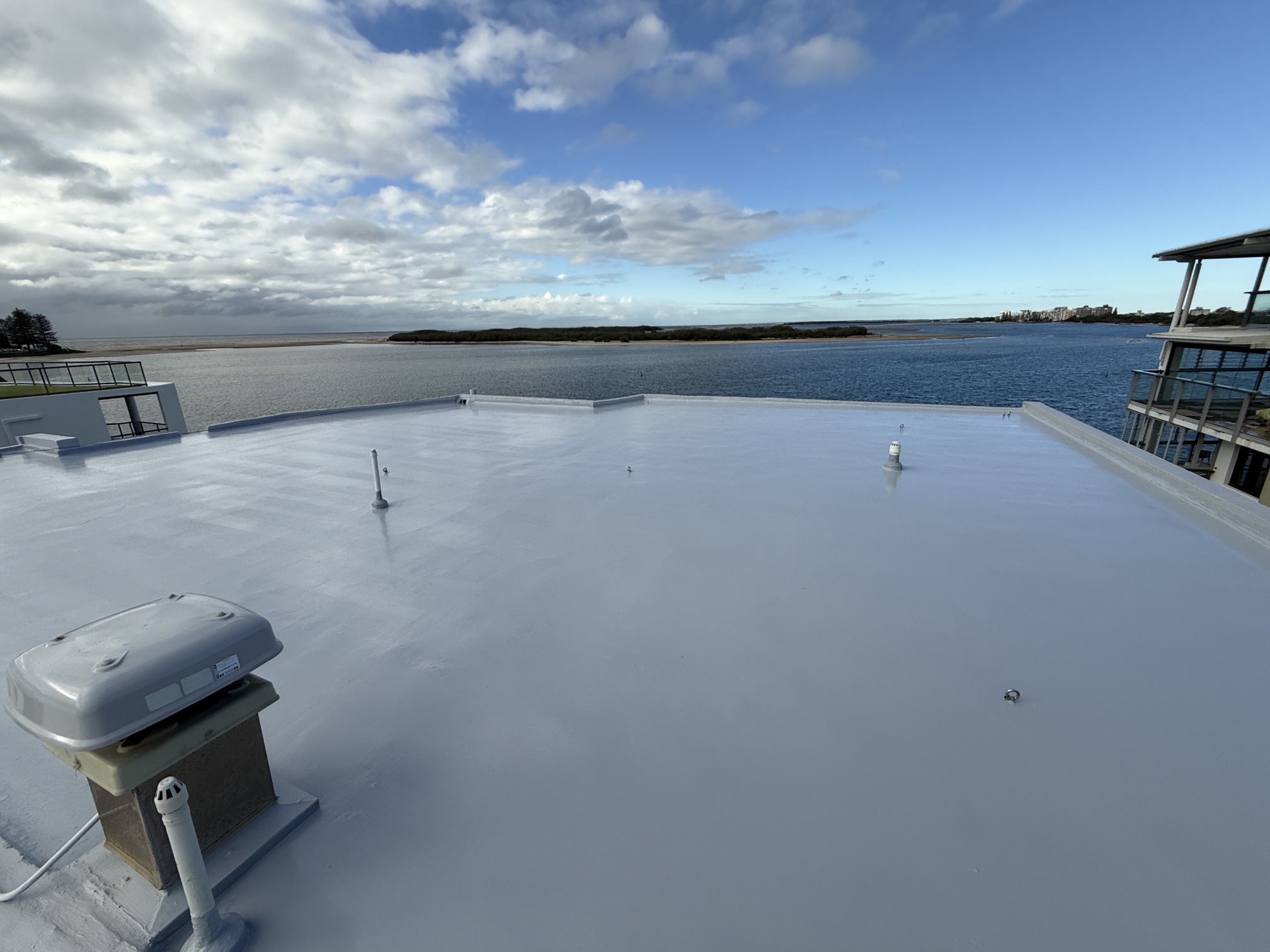
Reapplied the flashings & Works Completed
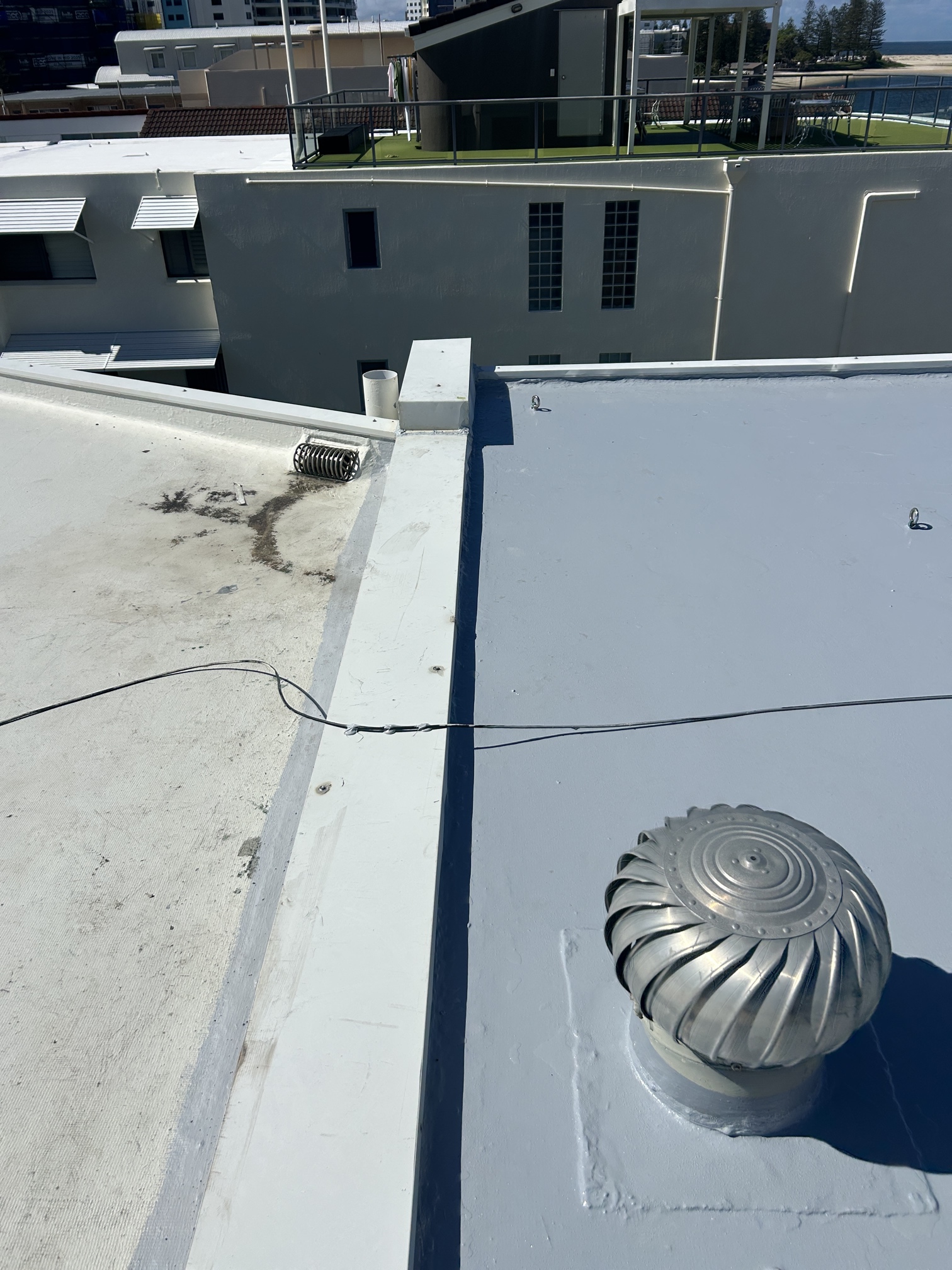
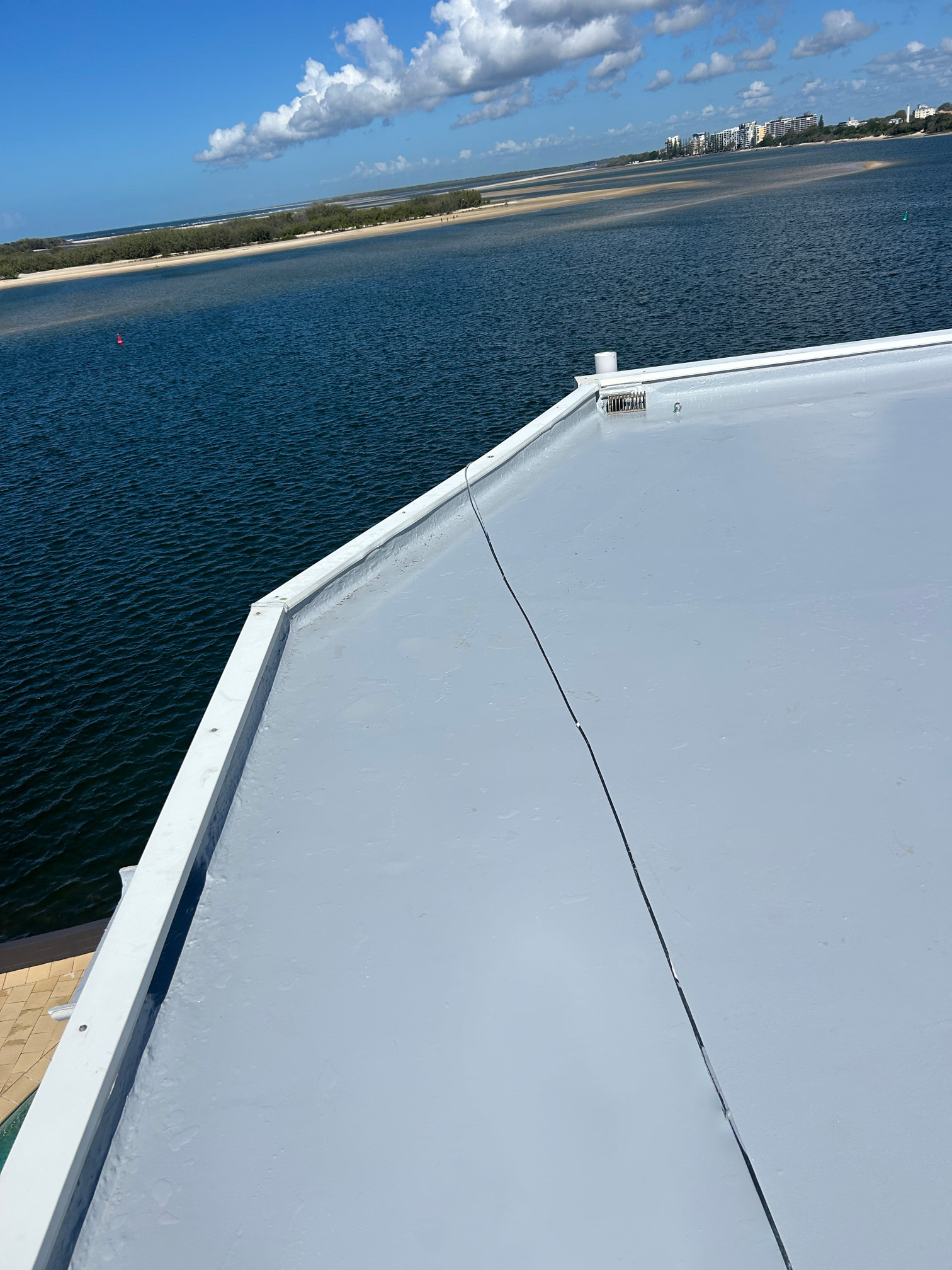
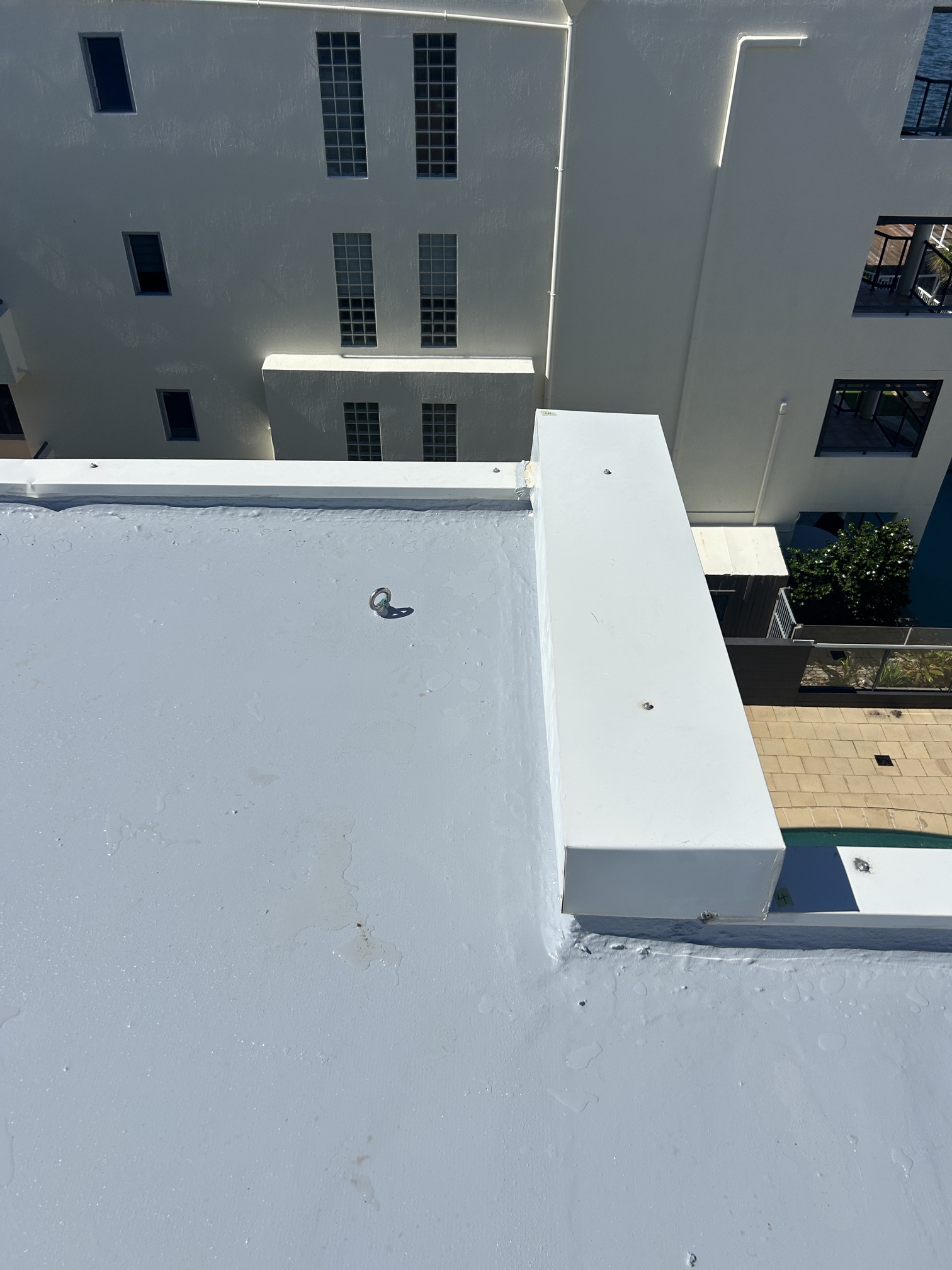
Related Services:
Membrane Waterproofing
Durable external annd internal membrane systems installed to reinforce waterproofing barriers and protect retaining walls, garages, and basements from persistent water ingress.
Planter Box Waterproofing
Membrane Waterproofing for planter boxes.
Specialist high-pressure crack injection using SNSeal
Injectable Sealant to permanently seal concrete cracks and prevent future water leaks.
Basement Waterproofing
Addressing active leaks in commercial and residential basement structures during or after excavation.
Retaining Wall Waterproofing
Treating cracked or leaking concrete and block retaining walls with non-invasive sealant systems.
Secant Pile Leak Sealing
Sealing water ingress through secant pile walls on coastal and high-groundwater sites using high-pressure injection methods.
Waterproofing Service Areas:
Australia-Wide, Key Areas include Queensland, Victoria & New South Wales
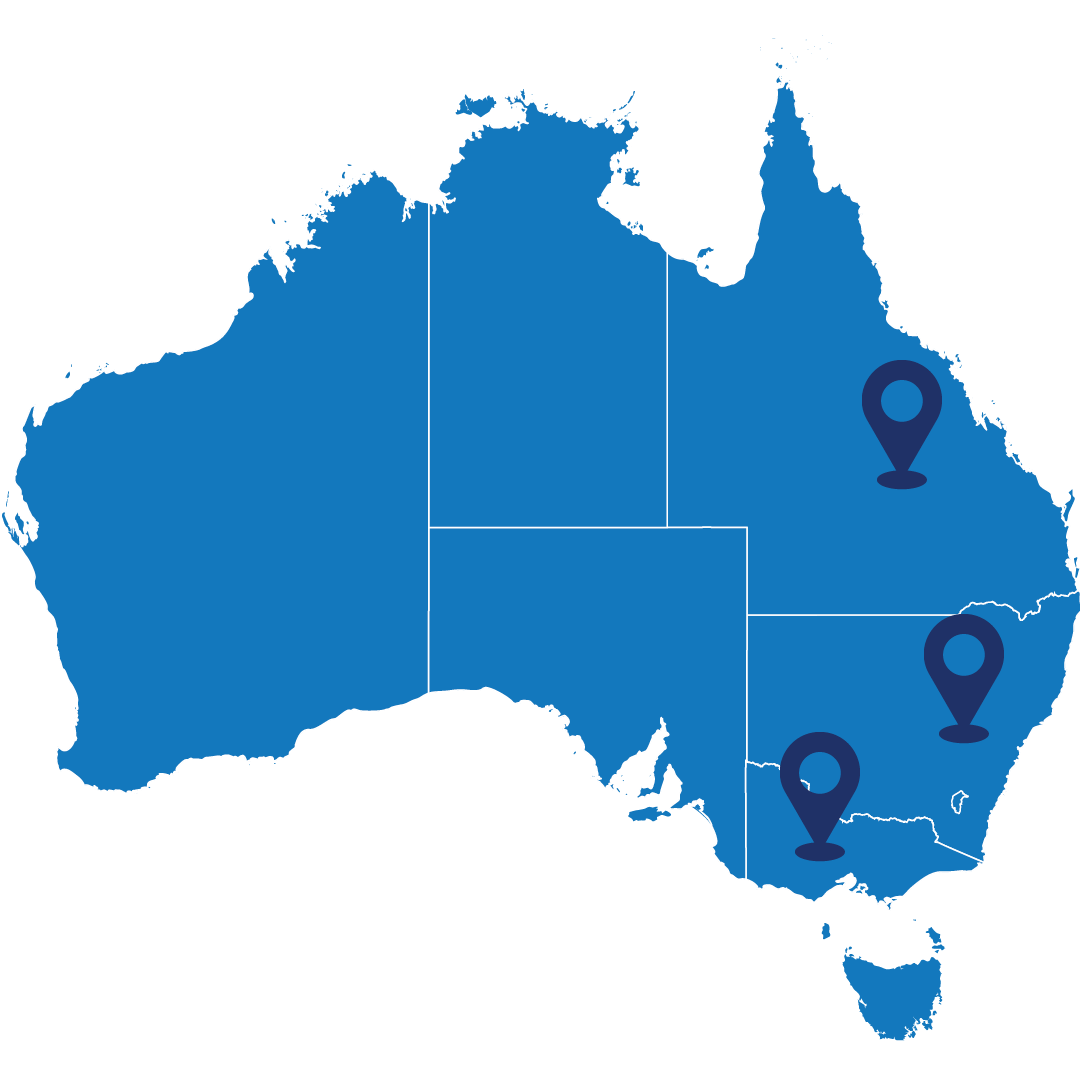
We provide waterproofing services Australia-wide, with our head office based on the Gold Coast. Our expert waterproofing solutions cover:
Queensland, including key service areas in Brisbane such as but not limited to Brisbane CBD, Fortitude Valley, Spring Hill, and West End, as well as Gold Coast areas like Southport, Surfers Paradise, Burleigh Heads, Coomera, Robina, and Tweed Heads. From injection waterproofing to membrane waterproofing, we offer a range of reliable solutions for both residential and commercial properties.
Victoria, we provide professional waterproofing services in Melbourne and surrounding areas, including but not limited to Melbourne CBD, Southbank, St Kilda, and Docklands. We also service other parts of Victoria, offering membrane waterproofing and other high-quality waterproofing solutions across regions such as Geelong, Werribee, Ballarat, and beyond. Our injection waterproofing methods ensure long-lasting protection for your property.
New South Wales, Our NSW Metro franchise is available to assist with all your waterproofing needs. From injection waterproofing to membrane waterproofing, we have the expertise to solve a wide range of waterproofing problems. You can reach our NSW Metro franchise directly at [email protected] or 0418 830 860.
Need Help with Concrete Cancer or Structural Damage on your Rooftop Podium?
If you’re seeing signs of cracking, spalling, or water-damaged concrete on your rooftop podium or notice mould growth in your unit below your rooftop, you may be experiencing some issues with your rooftop membrane or require an installation, get in touch to book a free on-site inspection and tailored repair solution.