Membrane Waterproofing
Your Trusted Membrane Waterproofing Experts
When you choose us for your membrane waterproofing needs, you’ll receive more than just quality workmanship. You’ll get expert advice tailored to your project. We take the time to understand your site conditions, walk you through the most suitable options, and explain exactly why they’ll work.
At Stop & Seal, we use high-performance polyurethane, cementitious and acrylic membranes across both new builds and remedial applications. From planter boxes and rooftops to wet areas, retaining walls and more, our systems are built to last and backed by manufacturer and applicator warranties of up to 15 years.
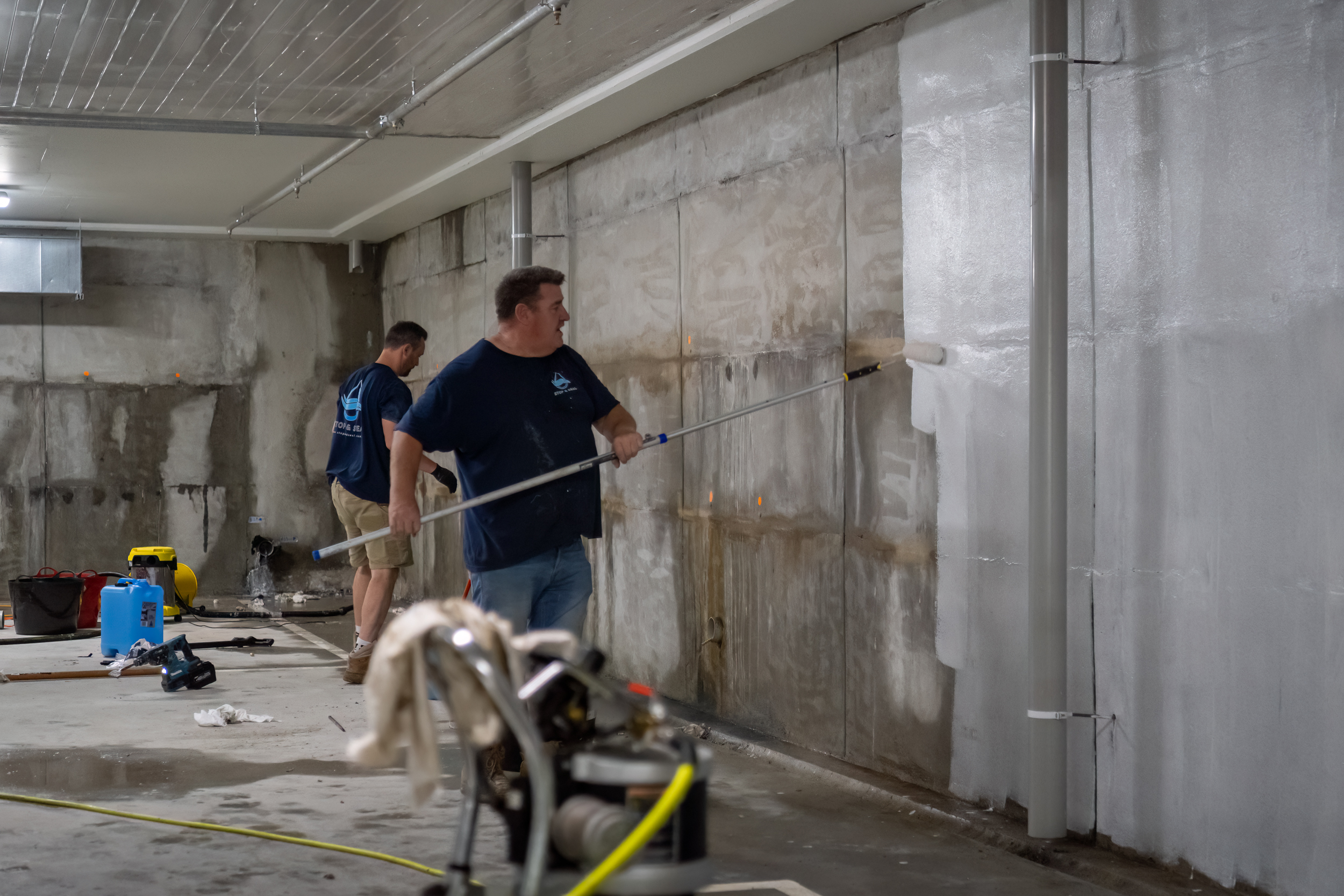
What Sets Us Apart
Expert Free Consultation & Honest Advice
We don’t just apply membranes, we help you understand them. Every project starts with a full free consultation to ensure you get the most suitable membrane waterproofing system for your specific needs.
Tailored Remedial & Preventative Solutions
From repairing failed membranes to installing complete new systems, we offer both remedial and preventative waterproofing designed to protect your property for the long haul.
Manufacturer-Approved Applicators
Our team is trained and approved by membrane manufacturers, ensuring every system is installed to the highest standard.
Up to 15-Year Warranty
We offer a combined Manufacturer/Applicator warranty of up to 15 years, giving you long-term confidence in the work we deliver.
Premium-Grade Membranes
Understanding Membrane Waterproofing
What is Membrane Waterproofing?
Membrane waterproofing is a technique used to prevent water from penetrating a structure by applying a seamless, watertight barrier over the surface. Depending on the product and environment, membranes may be sprayed, rolled, or poured. Once cured, they provide critical protection against leaks, water damage, and long-term structural degradation.
It’s a widely trusted solution across commercial and residential builds and a core part of modern waterproofing systems.
Choosing the Right Membrane
Waterproofing membrane success depends on more than just materials, it comes down to choosing the right system for the specific conditions of your project. With our industry knowledge and on-site experience, we make informed decisions that ensure long-term performance.
Our team ensures the membrane system we recommend is tailored to the unique conditions of each site. We offer a free consultation to walk you through our reasoning, so you’re confident that the system is fit for purpose.
Here’s what we take into account when choosing a membrane waterproofing system:
Purpose of the area
Is the surface going to be walked on regularly?
Will it hold planter boxes or other weight-bearing structures?
Each application demands different membrane properties, from trafficable finishes to root-resistant barriers.
Location
External areas are exposed to the elements: rainfall, UV rays, and temperature fluctuations can all affect membrane performance.
For example, an exposed rooftop may require a UV-stable topcoat.
Internal areas, like basements, often deal with hydrostatic pressure, especially in coastal regions where saltwater may also contribute to corrosion.
Long-term stresses
We consider long-term exposure factors like:
Constant moisture and root pressure in planter boxes.
Salt, heat, and humidity in coastal environments.
Movement and expansion in structural elements over time.
Where We Use Membrane Waterproofing
We install high-performance membrane systems across a wide range of internal and external applications of residential, commercial, and industrial sites:
Planter Boxes
Need root-resistant and moisture-tolerant membranes
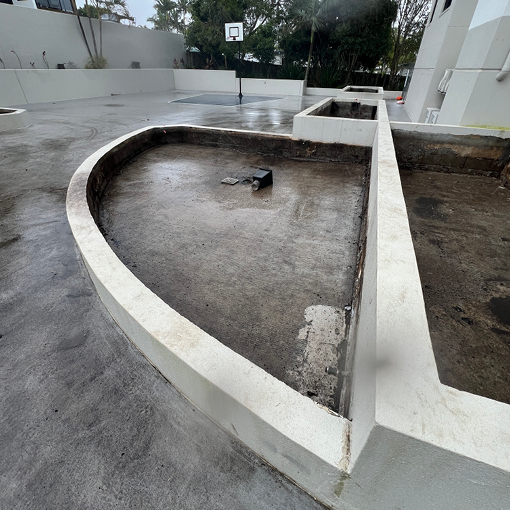
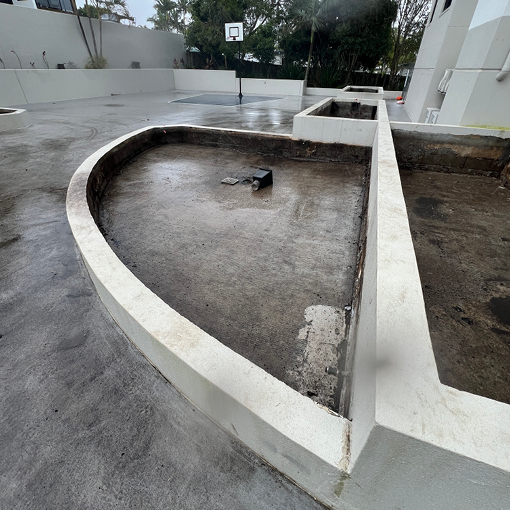
Before
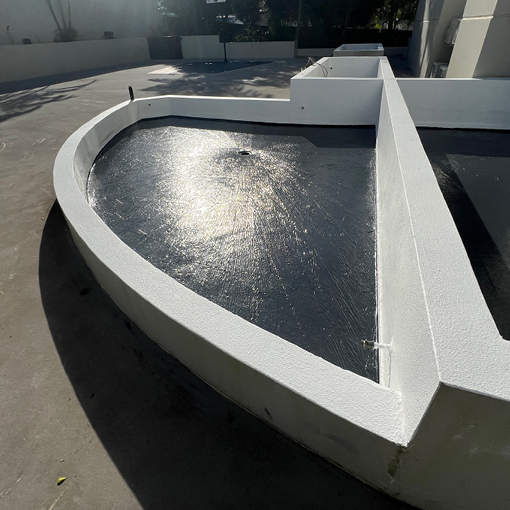
After
Rooftop & Podiums
Trafficable or non-trafficable, exposed to UV and weather.
Large-scale horizontal surfaces requiring layered protection
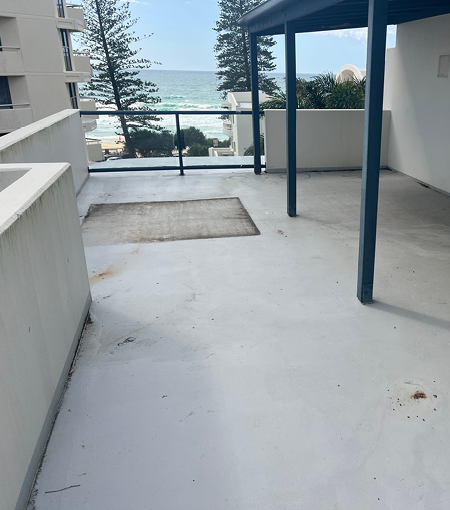
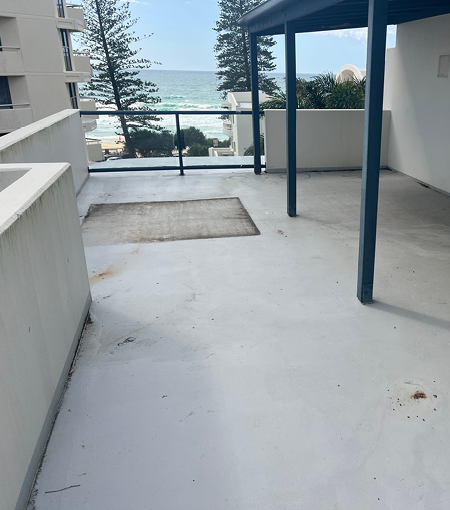
Before
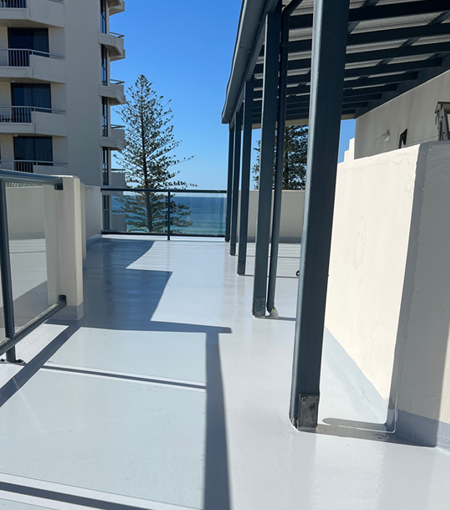
After
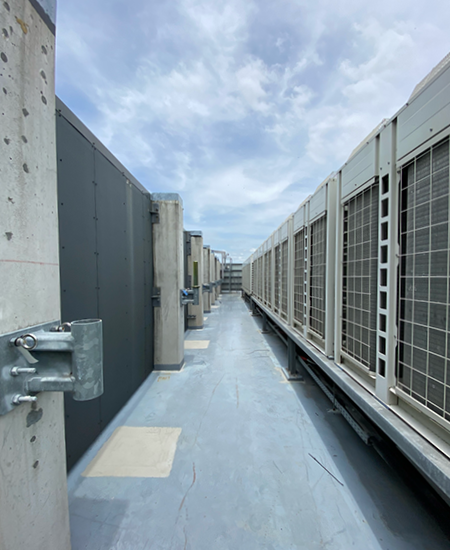
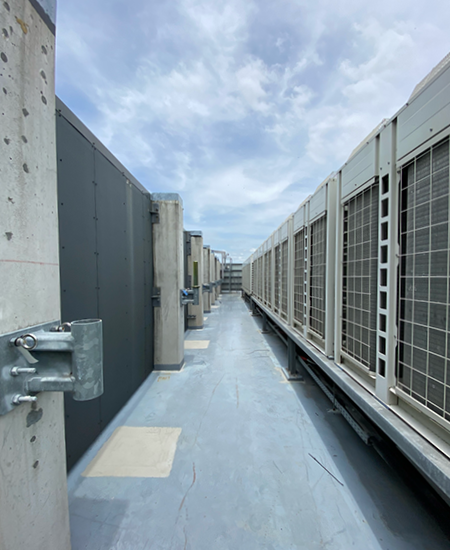
Before
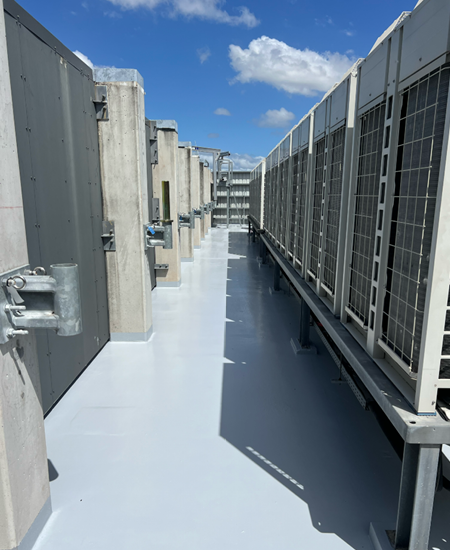
After
Carparks


Before
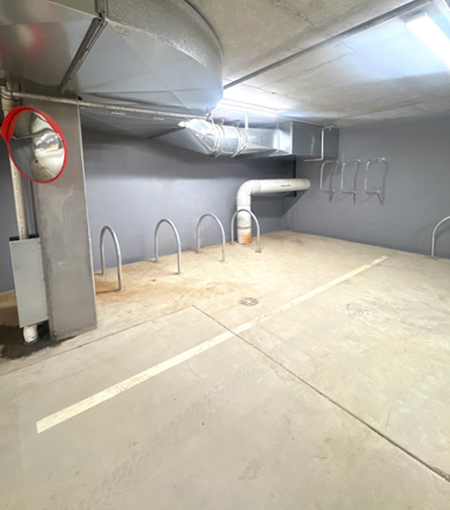
After
Soffit Slabs & Basement Ceilings
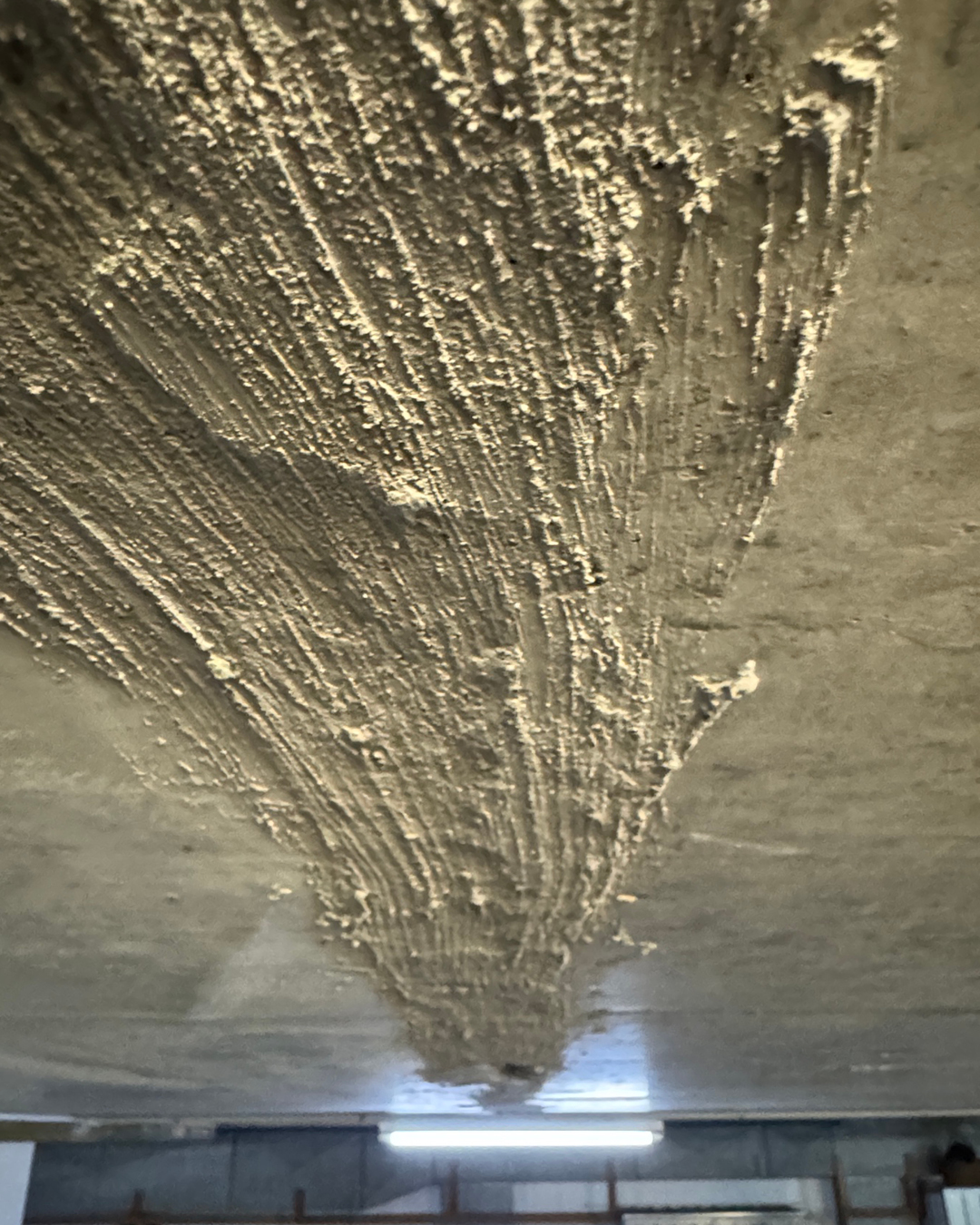
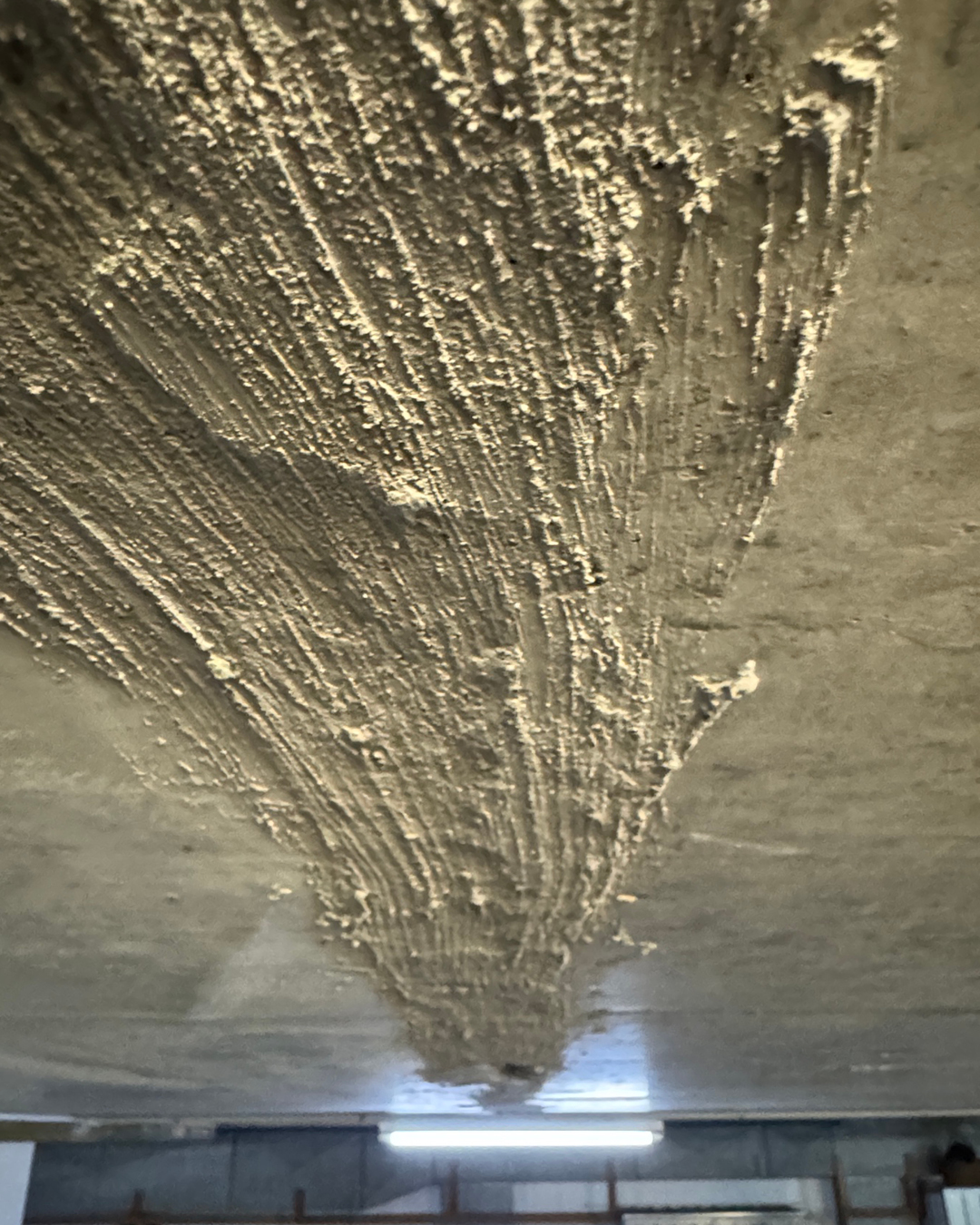
Before
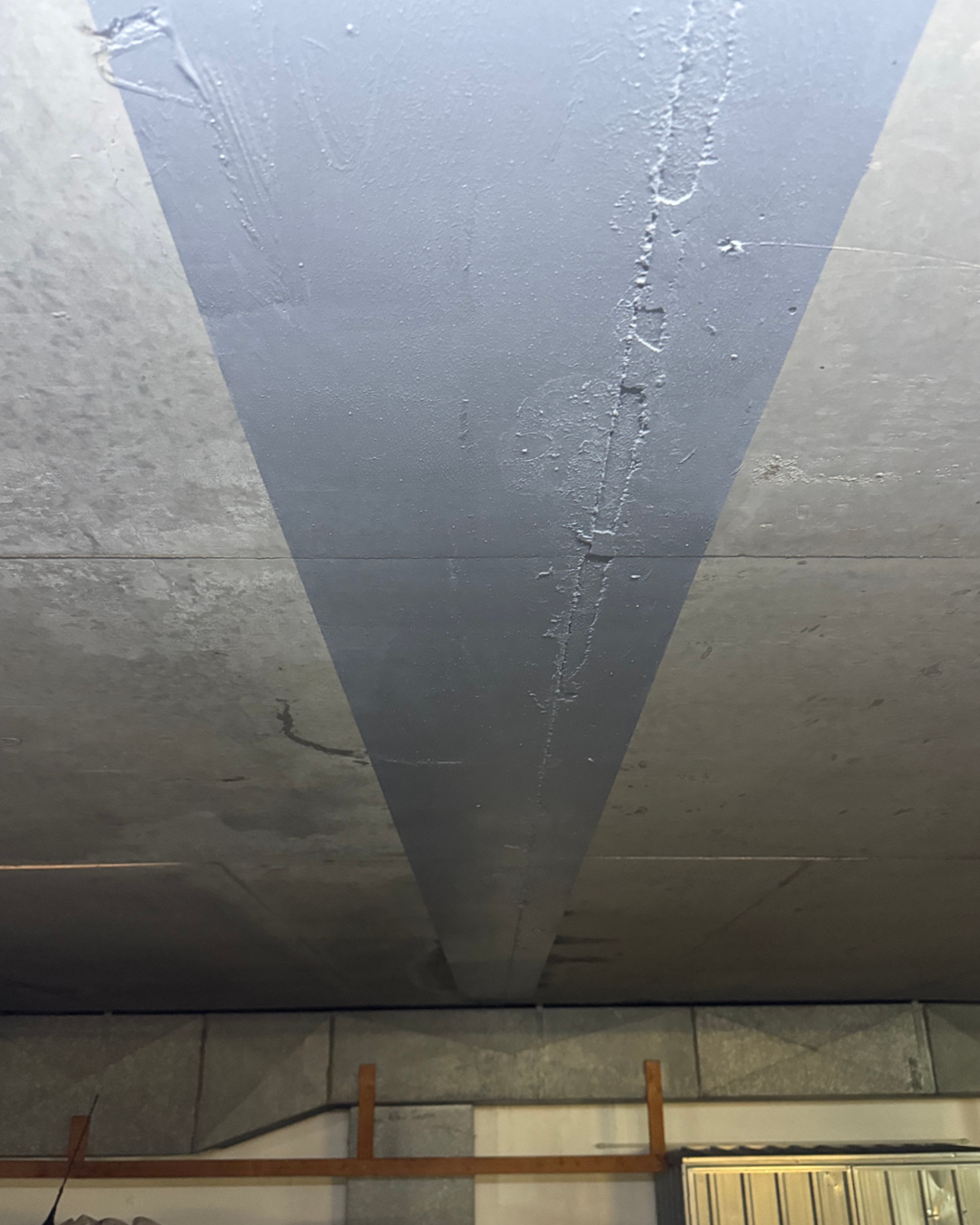
After
Retaining Wall
Below-ground or partially exposed walls requiring continuous waterproofing to prevent moisture intrusion and structural degradation
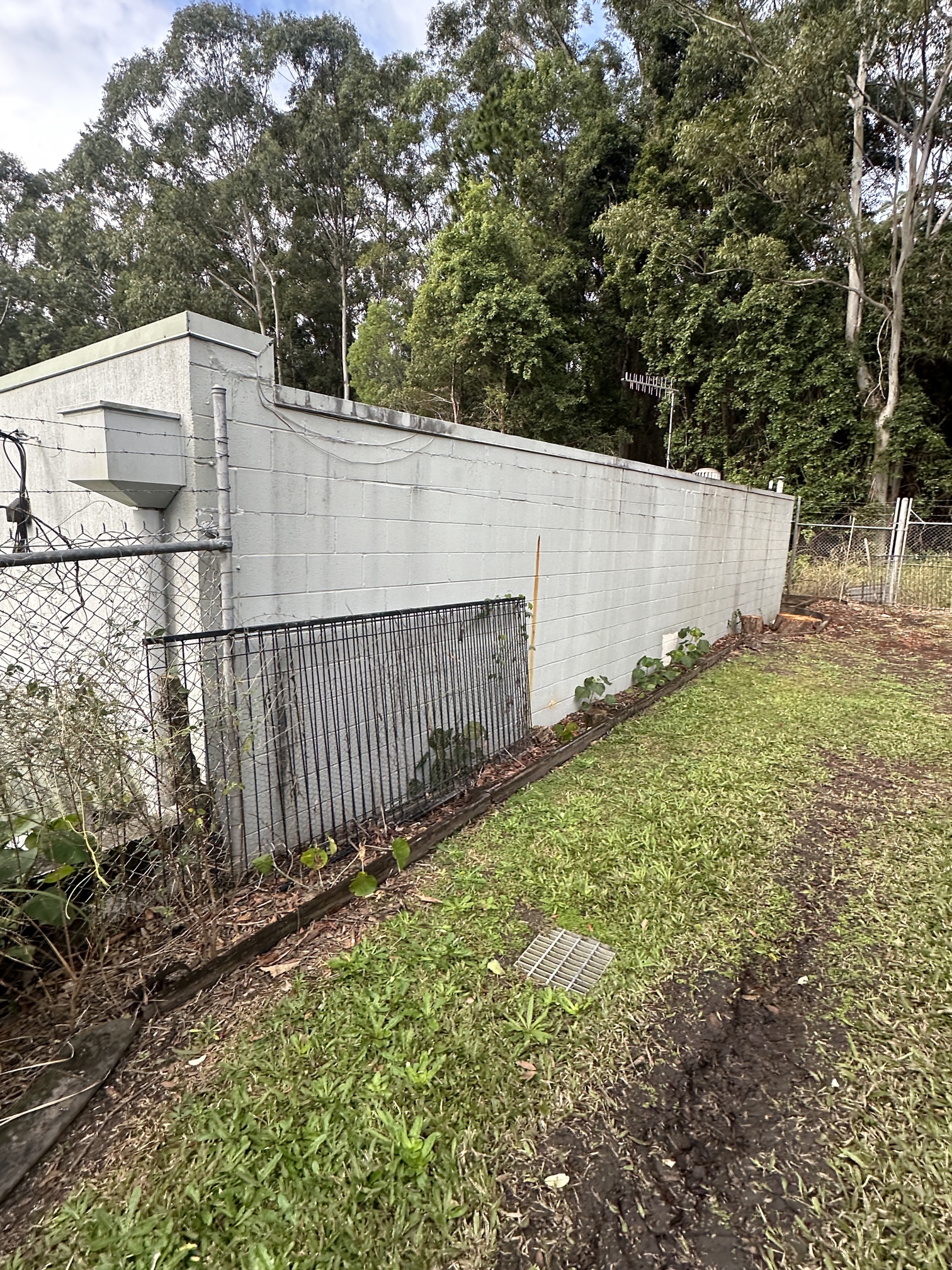
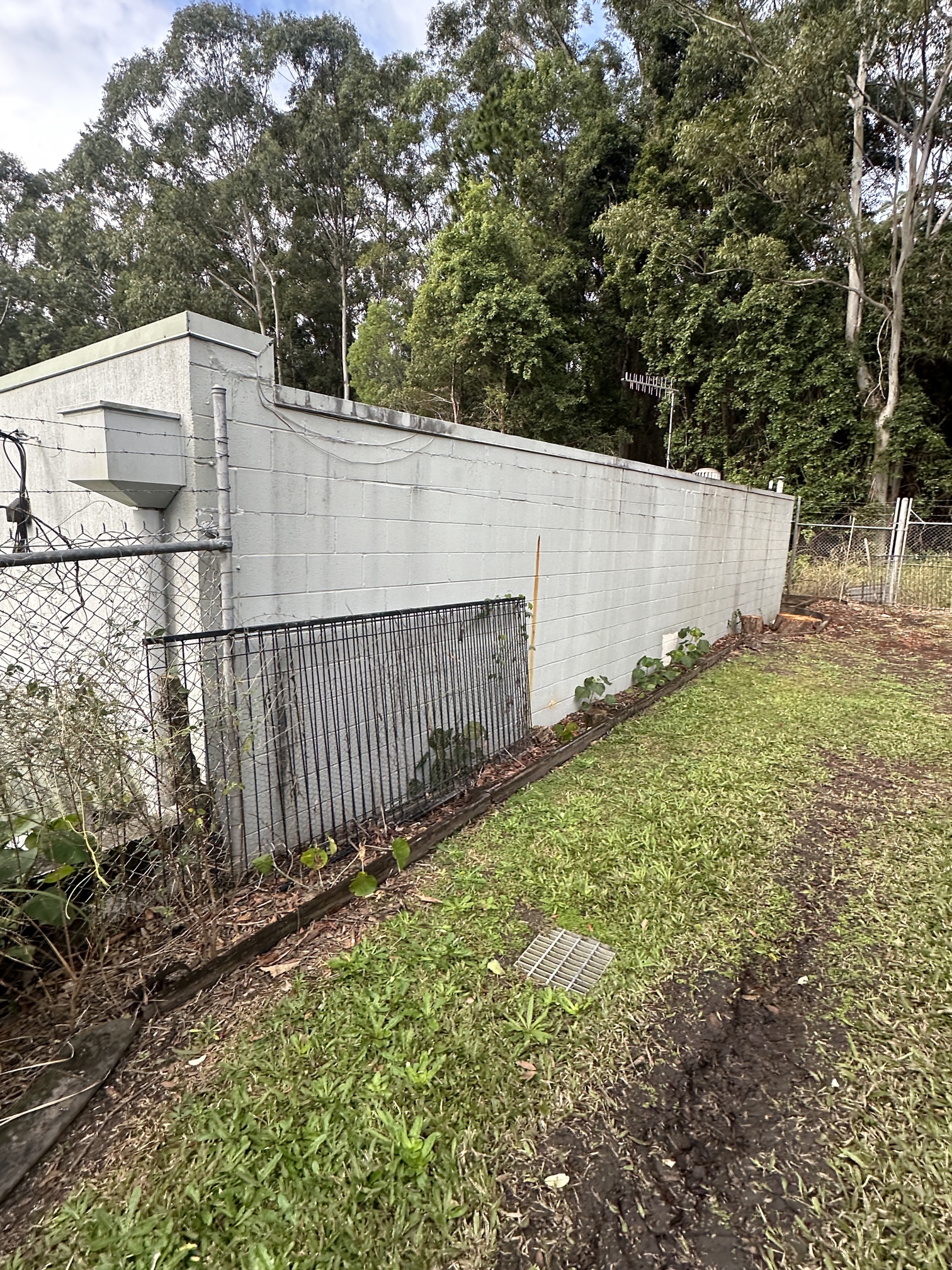
Before
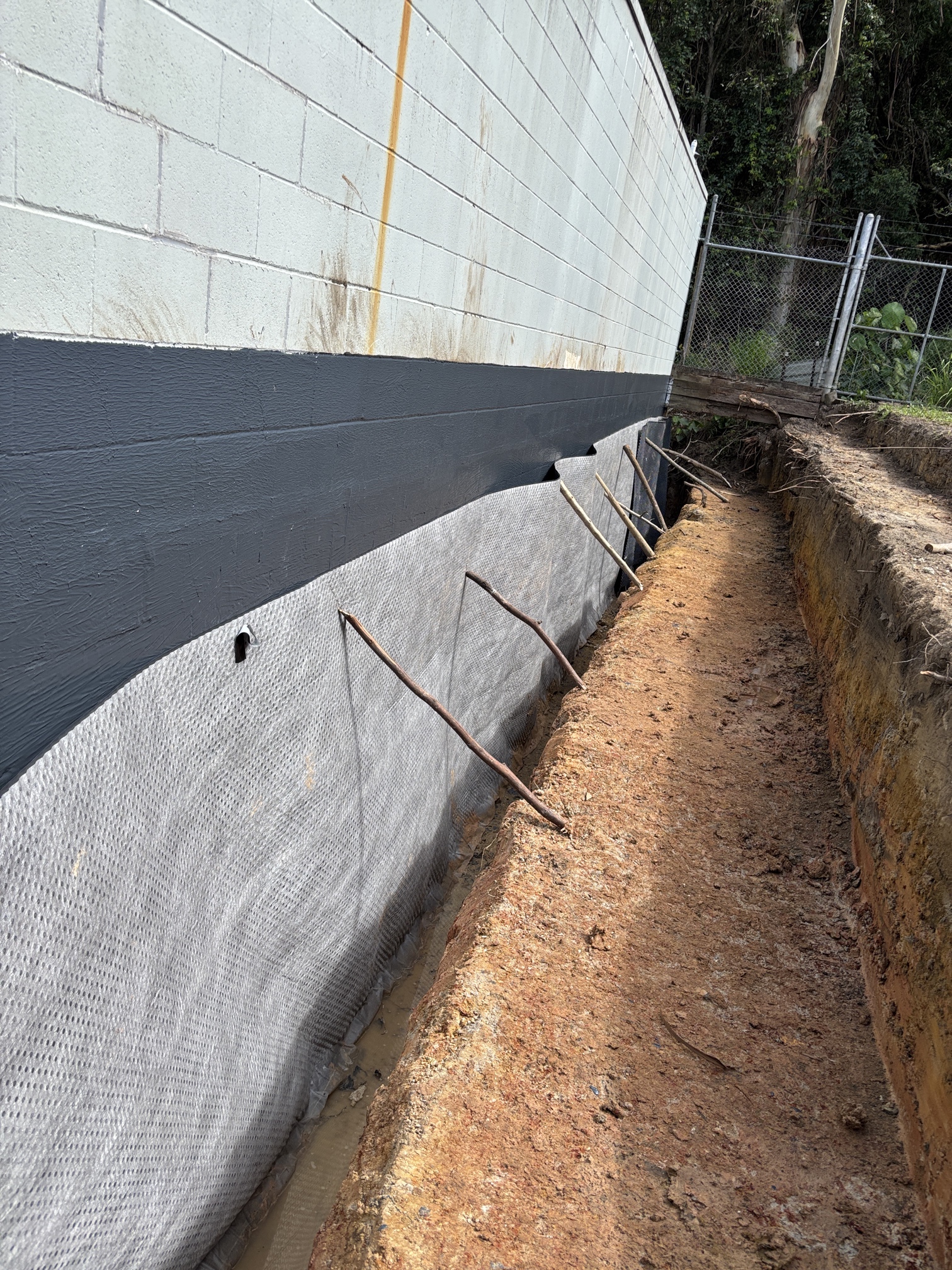
After
Lift Pits
Where below-ground water ingress is a risk
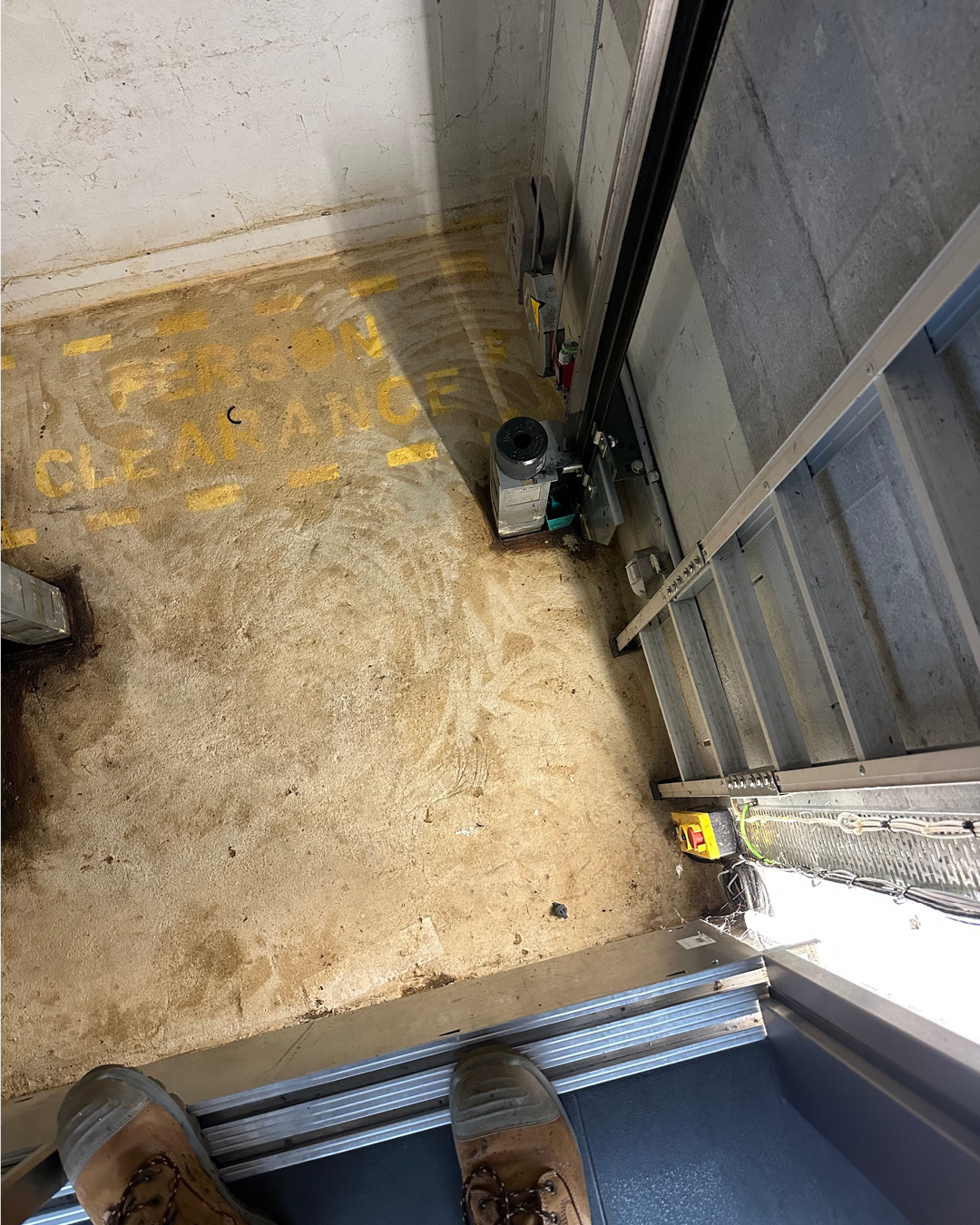
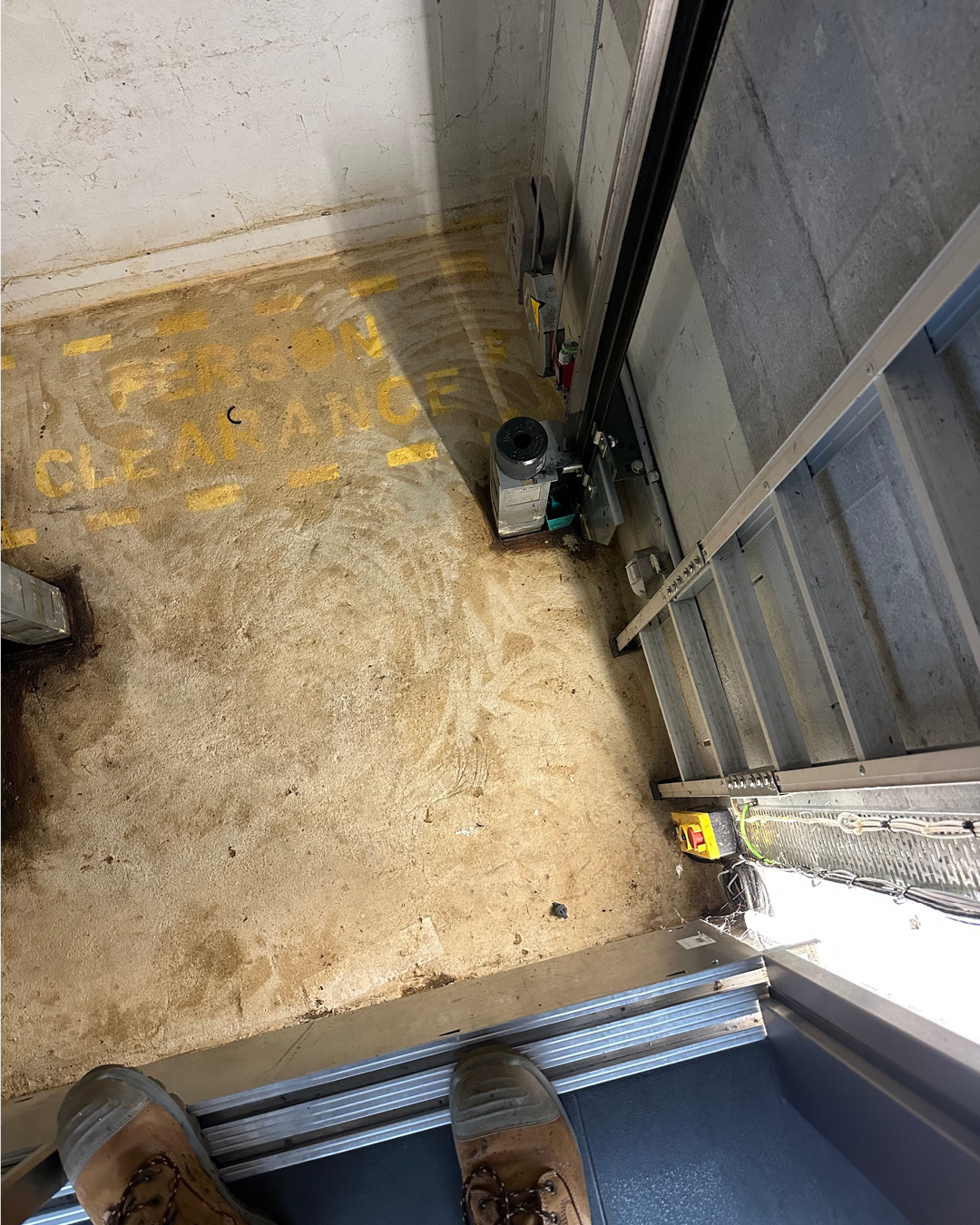
Before
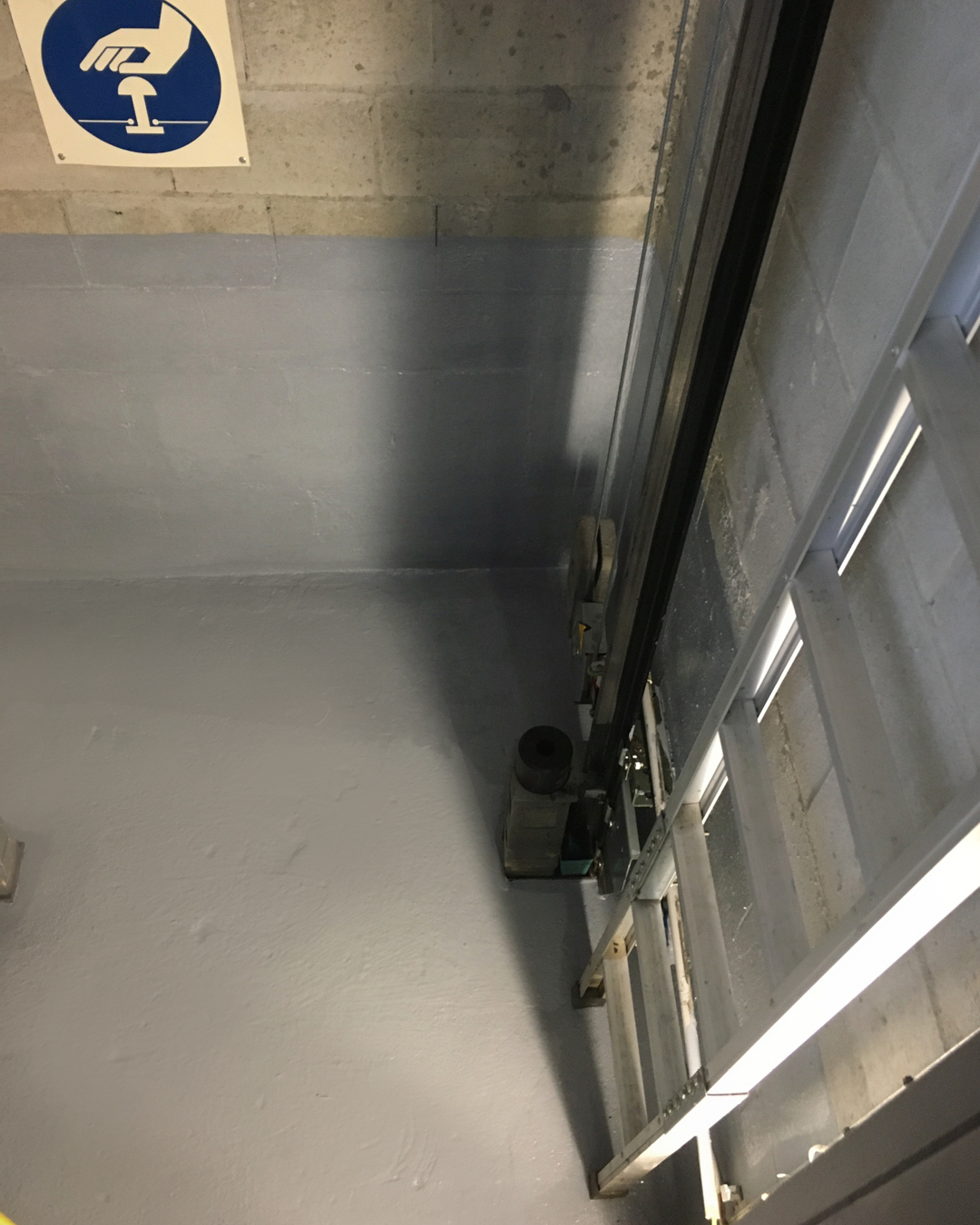
After
Why Do Some Membranes Fail?
Membrane failures generally fall into two categories: avoidable and inevitable.
Avoidable failures include
– Using a membrane that doesn’t meet the specific site requirements
Inevitable failures
Inevitable failures occur over time, even with the best system in place. Most membranes have a lifespan of around 15 years, with deterioration caused by:
– UV exposure
– Constant or heavy foot traffic
– Thermal expansion/contraction of the substrate
– Repetitive movement of equipment or objects
Signs Your Membrane is Failing:
Keep an eye out for clear signs such as bubbling, cracking, leaks, or staining. For a full breakdown of what to watch for, check out our blog post: Signs of Membrane Failure
Key Weak Points to Watch
Roof drains
Water tanks
Pipe penetrations
Cracking at the junction
Can You Just Patch a Failing Membrane?
In some cases, yes. But when failure is widespread or due to poor installation, patching isn’t enough. A full membrane rectification may be necessary for lasting protection. We’ll help you assess and advise the best long-term fix. (Blog: When Patching Isn’t Enough)
Key Weak Points to Watch
Roof drains
Water tanks
Pipe penetrations
Cracking at the junction